Temperatura e umidità: influenza di due parametri ambientali nella posa di un sistema resinoso
Le condizioni termo-igrometriche di cantiere influenzano la posa dei sistemi resinosi, incidendo su tempi di indurimento, adesione e resistenza. Monitorare temperatura e umidità evita difetti estetici e strutturali, garantendo prestazioni ottimali e durabilità del rivestimento. Vediamo perché.
Influenza delle condizioni termo-igrometriche sui sistemi resinosi per la posa a pavimento
Se mi chiedessero “qual è un vantaggio dei sistemi resinosi rispetto a soluzioni di rivestimento a base di elementi modulari da incollare o fissare meccanicamente?” una possibile risposta potrebbe essere il fatto che i sistemi resinosi vengono realizzati in opera distribuendo un prodotto allo stato fluido sulla superficie da trattare, come una seconda pelle che si adatta perfettamente alla forma del corpo sottostante. La stessa domanda rivolta al contrario, cioè quale potrebbe essere uno “svantaggio”, non escluderebbe la stessa risposta. La resina più o meno liquida che si applica sul supporto deve aderire e indurire perfettamente per conferire le caratteristiche prestazionali desiderate. Tutto questo lo fa ovviamente nell’ambiente di destinazione, le cui condizioni termo-igrometriche influiranno notevolmente sulla qualità del sistema indurito.
Il controllo delle condizioni ambientali di cantiere è quindi un’operazione necessaria e fondamentale per evitare possibili problemi estetici o prestazionali al sistema resinoso. Tale verifica dovrebbe essere effettuata almeno tre volte nell’arco della giornata lavorativa: all’inizio, a metà e alla fine delle fasi di posa.
Gli strumenti necessari sono ormai semplicissimi da usare, molto affidabili e forniscono i dati in tempo reale. Esistono anche piccoli strumenti portatili in grado di registrare questi parametri a intervalli regolari durante l’arco di tutta la giornata. I dati vengono poi scaricati su un computer a costituire un archivio storico delle condizioni di cantiere, sia nelle fasi di posa che in quelle di indurimento, utile nel caso si volesse indagare in merito ad eventuali problemi di carattere estetico o funzionale sul sistema resinoso.
Ma cosa bisogna controllare, e perché?
La risposta sul “cosa” è semplice. I parametri da misurare riguardano le temperature dell’aria, della superficie di posa e del materiale, a cui si aggiunge il valore dell’umidità relativa dell’aria. Non includo in questo contesto il controllo del contenuto di umidità del supporto, operazione fondamentale per la buona scelta e riuscita del sistema resinoso. Tale valore deve essere rilevato già in fase preventiva e necessita di un trattato a parte; vedo già la nostra redattrice affilarsi le unghie sulla mola per convincermi a scriverlo.
Ma per quanto riguarda il “perché”? In che modo e in che misura le temperature e l’umidità relativa prima citate possono influire sulle fasi di posa e sulla qualità finale di un sistema resinoso?
Mettiamoci comodi, e facciamo un breve ripasso delle nostre nozioni di chimica e fisica.
L'influenza della temperatura ambientale sui sistemi in resina
Le tipologie di resine maggiormente utilizzate sono costituite da due, talvolta tre, componenti da miscelare tra loro prima dell’applicazione. Dal momento della loro intima miscelazione i due o più componenti cominciano a reagire chimicamente per dare un materiale resinoso indurito dotato delle caratteristiche richieste.
Ad esempio, l’eposside andrà a reagire con la sua amata poliammina o i composti a base di isocianato si uniranno a qualche poliolo che si trova per caso a passare nei paraggi. Come per ogni buona reazione chimica che si conosca, il carattere cinetico con la quale avviene questa unione è fortemente influenzato dalla temperatura. Al crescere di quest’ultima aumenta, ovviamente, la velocità di reazione. Non solo, anche la quantità di reagenti che partecipano alla reazione, che non potrà mai essere il 100% assoluto, sarà maggiore.
Le resine epossidiche e poliuretaniche utilizzate per realizzare i sistemi resinosi reagiscono correttamente entro un intervallo di temperatura normalmente compreso tra i +8/10°C e i +30/35°C, stabilito dal produttore. Applicare un sistema resinoso al di fuori di questi limiti può comportare problemi di tempistiche di cantiere e qualità del sistema finito. Alle basse temperature i tempi di indurimento e di attesa tra i vari strati dei materiali si allungano drasticamente assumendo caratteri biblici e sul versante opposto, con temperature elevate, si possono riscontrare difficoltà di posa dei materiali a causa del breve tempo di utilizzo dopo la miscelazione prima che inizi la fase di gel.
La temperatura di reazione può anche influenzare la forma della struttura tridimensionale che le molecole vanno a costituire unendosi tra loro. La complessità di tale struttura caratterizza le proprietà fisiche e di resistenza chimica del prodotto resinoso indurito. Tale forma è irreversibile, se parte e continua male, ad esempio quando si applica la resina al disotto del limite minimo di temperatura, non si può più tornare indietro. Un successivo innalzamento termico non risolverebbe il problema; ormai il danno è fatto, ciò che è partito male non può che finire peggio.
Riassumendo quindi un concetto semplice ma molto importante, applicare le resine a temperature al di sotto della soglia minima consentita non solo influisce sui tempi di realizzazione e di indurimento del sistema resinoso, che diventano particolarmente lunghi, ma comporta spesso anche una reazione chimicamente incompleta, e probabilmente strutturata male, tra i vari componenti delle resine. Ne consegue un netto calo delle prestazioni finali del sistema resinoso e potenziali problemi di sbiancamento che verranno descritti meglio nei prossimi capitoli.
Le temperature che maggiormente influenzano la velocità di reazione sono quelle relative al supporto e all’aria. La temperatura del materiale può aiutare un innesco di reazione più o meno rapido, ma gioca un ruolo fondamentale per altri motivi. Riveste un importante ruolo in quanto da essa dipende la maggiore o minore fluidità dei materiali e, di conseguenze, la loro facilità di miscelazione e posa. Una regola molto empirica dice che un incremento di temperatura di 10°C riduce di circa la metà il valore della viscosità di un prodotto resinoso. Numeri reali a parte, è un dato di fatto che le operazioni di preparazione e posa di una resina che ha una temperatura di +20°C siano nettamente più agevoli rispetto alla stessa resina a +10°C.
In cantiere si dovrebbe disporre di un locale climatizzato, o di una piccola serra fatta apposta, con una temperatura compresa tra i +18°C e i +25°C – grado più, grado meno – per mantenere i prodotti resinosi da applicare in un intervallo che ne renda agevole l’utilizzo (quindi non troppo freddi) ma che mantengano, una volta miscelati, un tempo di vita utile o pot-life che non ne complichi la posa perché troppo breve (quindi non troppo caldi). Esaurita la procedura di posa, il valore della temperatura del materiale, con qualche eccezione ad esempio per i sistemi a massetto ad alte resistenze, tende a perdere la sua importanza, perché acquisirà quella dell’ambiente circostante. Ai fini dei tempi e della qualità dell’indurimento non serve a molto applicare una resina inizialmente a +20°C su un pavimento in calcestruzzo che si trova a +5°C con una temperatura dell’aria a +4°C. In un caso simile, qualche problema sul sistema finito ce lo dobbiamo comunque aspettare.
Il tema della bassa temperatura ambientale è un punto di forza per i sistemi resinosi realizzati con prodotti a base di polimetilmetacrilato (PMMA). La reazione di polimerizzazione avviene grazie a un innesco causato dall’aggiunta di uno specifico catalizzatore a base di perossido, dosato in funzione della temperatura.
Questi prodotti possono essere applicati anche a temperature di -5°C senza problemi, ma aggiungendo un apposito accelerante si può perfino scendere fino a -20/25°C.
Anche i prodotti resinosi monocomponenti, che possono includere alcune vernici e finiture, risentono della temperatura. Il loro indurimento avviene spesso per evaporazione di un diluente o disperdente, compresa l’acqua, consentendo l'avvicinamento tra loro delle particelle di resina che grazie alle forze elettriche interne si attraggono l'una con l'altra. La capacità di deformarsi delle particelle e la presenza del diluente come mezzo di movimento permettono alle stesse di unirsi e di fondersi in un unico strato. Questo generico processo è noto col nome di coalescenza ed è importante sapere, nel campo delle vernici, che avviene solo se le molecole che si stanno avvicinando tra loro hanno una certa “plasticità” che ne permette la possibilità di compattarsi.
Esiste una soglia di temperatura, detta temperatura minima di filmazione, al di sotto della quale le particelle di resina sono troppo viscose e indeformabili; il solvente che le disperde evaporerebbe comunque, ma il risultato finale sarebbe un prodotto non compattato e non coeso, con tanti vuoti tra le molecole. Come per i casi prima descritti, un innalzamento della temperatura non risolverebbe il problema, perché anche se le particelle di resina diventassero meno viscose verrebbe a mancare l’effetto di reciproco avvicinamento dovuto all’evaporazione del solvente. Questa categoria di resine non include quei prodotti igroindurenti che sembrano essere monocomponenti, e dal punto di vista pratico e commerciale lo sono essendo costituiti da una sola latta di materiale, ma che sono in realtà più chimicamente analoghi alle resine bicomponenti, in quanto induriscono grazie alla reazione che avviene con l’umidità dell’aria.
Fin ad ora abbiamo visto come la temperatura possa influire direttamente sulle fasi di posa e sulla qualità del sistema resinoso finito, ma vi è un secondo fattore di importanza rilevante che potremmo definire indiretto, in quanto in co-partecipazione con un altro attore appena citato…
L'influenza dell'umidità dell’aria sui sistemi in resina
Temperatura e umidità dell’aria sono due entità inscindibili, vivono l’una con l’altra e si influenzano reciprocamente in una danza eterna che l’uomo è riuscito a descrivere tracciando alcune linee su un foglio di carta cui ha dato il nome di diagramma psicrometrico qui sotto visualizzato.
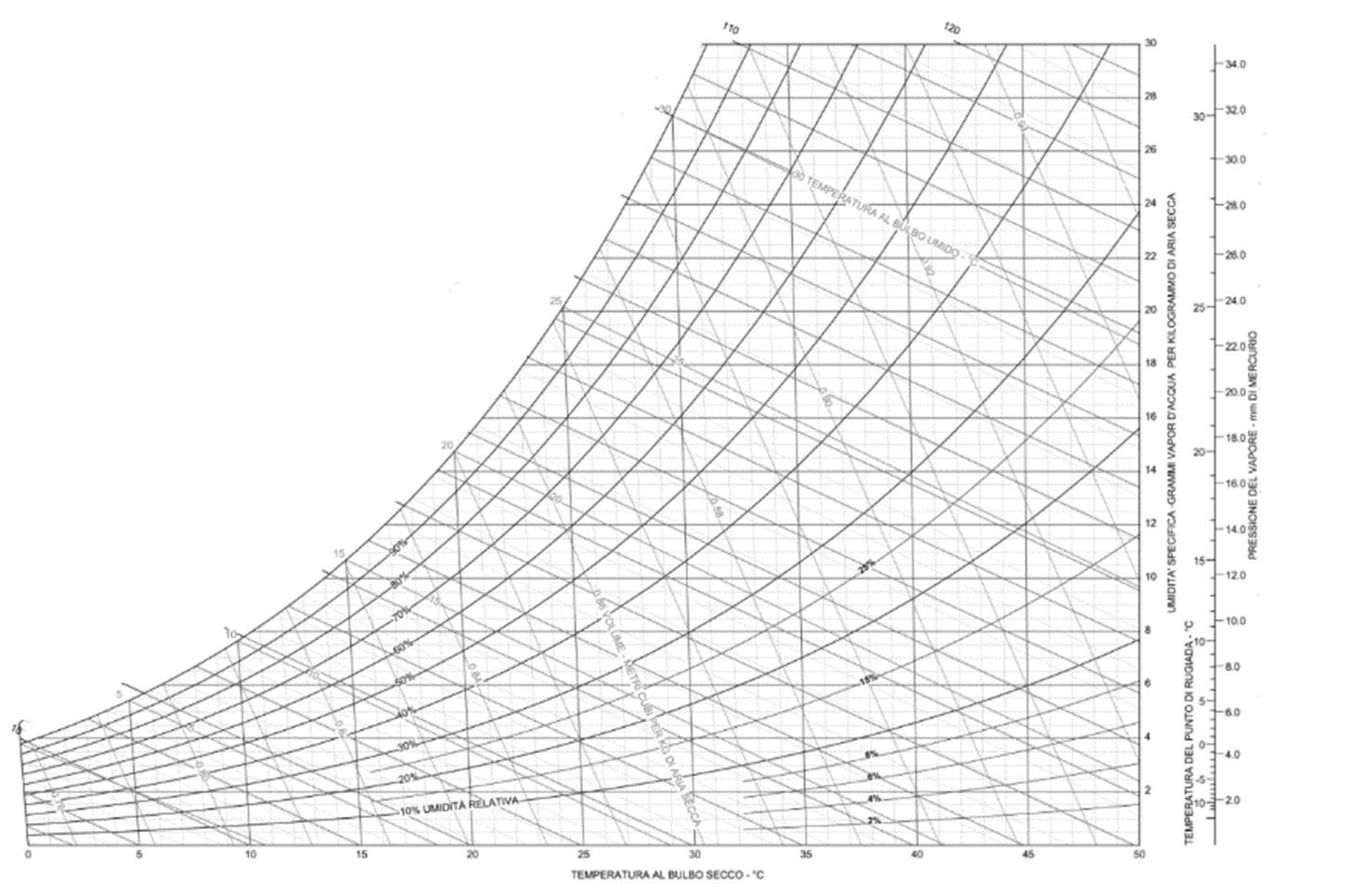
Non lo si confonda col diagramma “psicometrico”, come talvolta l’ho sentito chiamare... Mentre il primo rappresenta le diverse condizioni in cui si trovano l’aria ed il vapore acqueo in essa contenuta in funzione della temperatura, il secondo è un grafico molto più semplice e intuitivo che mette in relazione il bisogno di ferie (in ordinata) in funzione dello stress (in ascissa). La pendenza della curva è molto soggettiva…
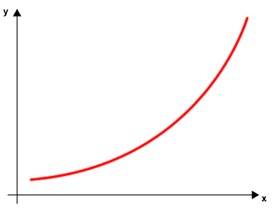
Tornando a quello che ci interessa di più, il diagramma psicrometrico ci dice, tra le tante informazioni contenute, quale sia la temperatura di condensa ad una determinata situazione di umidità e temperatura dell’aria.
La conoscenza e il monitoraggio di questi parametri in cantiere sono fondamentali per valutare il rischio di presenza di eventuale condensa sulle superfici di posa o sugli strati resinosi appena applicati e ancora in fase di indurimento. La misurazione si effettua con strumenti semplici e affidabili che ci forniscono anche il punto di condensa relativamente alle condizioni misurate. Il corredo di strumenti da tenere in cantiere si completa con un termometro per superfici col quale si misura la temperatura del supporto, che non deve mai essere uguale o minore di quella del punto di rugiada. La formazione di condensa deve essere assolutamente evitata, almeno fino a quando il sistema resinoso non avrà raggiunto un buon grado di indurimento.
Non basta avere una temperatura del supporto appena più alta del punto di condensa indicatoci dal grafico o dal termoigrometro; le variabili climatiche e di cantiere, le tolleranze nelle letture degli strumenti, il rischio di repentini cambiamenti delle condizioni termo-igrometriche dell’aria anche a causa di operazioni e attività umane e la naturale tendenza a prendersi un buon margine di sicurezza fanno sì che la temperatura della superficie di posa venga considerata “sicura” se maggiore di almeno 3°C rispetto al punto di condensa.
A parità di temperatura dell’aria, al diminuire dell’umidità relativa si riduce il valore della temperatura di condensa. Traducendo in pratica questa acuta osservazione, realizziamo che applicare un sistema resinoso con umidità relativa ambientale minore del 50% non sarebbe un problema neanche se il supporto avesse una temperatura di 6-7°C minore di quella dell’aria, che sarebbe una condizione piuttosto rara; si rispetterebbero comunque i 3°C di margine di sicurezza prima citati. Con un’umidità del 60% bisogna prestare molta più attenzione, con un valore al 70% devono suonare molti campanelli d’allarme e con un valore dell’80% - come si può anche facilmente rilevare dal diagramma – la temperatura di condensa si trova esattamente 3°C sotto la temperatura dell’aria, al netto di qualche ininfluente decimale, pertanto il supporto dovrebbe risultare più caldo dell’aria stessa, condizione ancora più rara della precedente.
Il valore limite massimo di umidità relativa dell’aria durante le fasi di posa e indurimento del sistema resinoso viene spesso indicato dal produttore dei materiali in 80%. Che sia per il motivo poc’anzi descritto è probabile, ma non importante se poi tale limite non viene letto o interpretato correttamente.
Personalmente ho visto applicare resine durante giornate di pioggia; vero è che le condizioni termo-igrometriche dell’area di cantiere possono essere leggermente diverse da quelle esterne, anche in assenza di impianti di condizionamento dell’aria, ma quante volte capita che si anteponga l’esigenza di consegnare il lavoro finito alla sicurezza di eseguire correttamente tutte le fasi di posa?
Ma questa condensa è poi così terribile se si forma?... Lo è quasi sempre, al netto di tutte le variabili di formulazione dei materiali utilizzati e della quantità di condensa prodotta. L’utilizzo di resine in dispersione acquosa può risultare meno suscettibile a subire problemi e con limiti di tolleranza sensibilmente maggiori, ma è una convinzione sopravalutata che può portare a risultati spiacevoli.
Vediamo come possono influire le condense su un sistema resinoso.
[...] CONTINUA LA LETTURA NEL PDF IN ALLEGATO
Il testo analizza l’influenza della condensa nei sistemi resinosi, evidenziandone gli effetti negativi su adesione, estetica e funzionalità del rivestimento.
Controlli e Diagnostica
Una raccolta di approfondimenti per chi si occupa di fare controlli e verifiche dei materiali nel settore delle costruzioni e dell'edilizia.
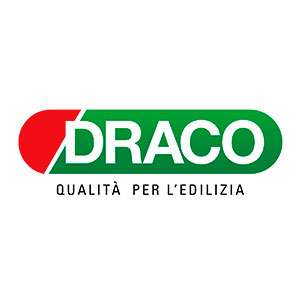
Pavimenti Industriali
Con il topic "pavimento industriale" vengono raccolti tutti gli articoli pubblicati sul Ingenio su queste tipologie di pavimentazioni in calcestruzzo e riguardanti la normativa, la progettazione, l'applicazione, l'innovazione tecnica, i casi studio, i controlli e i pareri degli esperti.

Pavimenti per Interni
Tutto quello che devi sapere sulle pavimentazioni per interni: le tipologie di rivestimento più comuni, le soluzioni tecniche più innovative, gli...
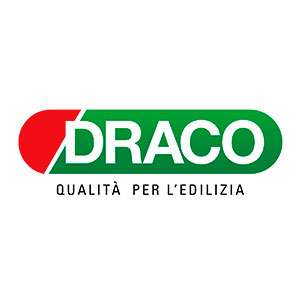
Resina
I sistemi resinosi continui rappresentano una versatile gamma di soluzioni per la protezione e il miglioramento delle caratteristiche delle...
Condividi su: Facebook LinkedIn Twitter WhatsApp