Stima della resistenza dell’acciaio delle barre di armatura in opera mediante prova di durezza Leeb
Stima della resistenza dell’acciaio delle barre di armatura inglobate in getti di calcestruzzo mediante la prova non distruttiva di durezza in opera Leeb
Per conseguire i livelli di conoscenza previsti dalle N.T.C., per le strutture in calcestruzzo armato è necessario risalire alle caratteristiche di resistenza dell’acciaio delle barre di armatura in opera. Tale operazione prevede l’estrazione di diversi campioni di armatura dagli elementi strutturali, per sottoporre gli stessi a prova di trazione: in tal modo sarà possibile individuare per ogni campione lo snervamento, la rottura e l’allungamento percentuale.
L’estrazione di una barra di armatura da una struttura in c.a. in opera ovviamente è una operazione molto “traumatica” per l’elemento strutturale: demolizione del copriferro e del calcestruzzo attorno alla barra, rilascio tensionale nella barra, ridistribuzione delle tensioni, ripristino della continuità della barra in opera complesso e soggetto ad imperfezioni, ecc.
Al fine di capire se è possibile ridurre la numerosità di prelievi di barre dagli elementi in c.a. in opera in questo lavoro si è voluto studiare come poter effettuare una classificazione di massima dell’acciaio da c.a. con una prova non distruttiva e di facile esecuzione: la misura della durezza dell’acciaio utilizzando un durometro Leeb.
La prova di durezza Leeb è un metodo di prova dinamico per la determinazione della durezza dell’acciaio: il tondo d’acciaio, inglobato in un getto di calcestruzzo, presenta caratteristiche interessanti per l’applicazione della prova Leeb in relazione alla massa e rigidezza che offre in tale configurazione, requisito essenziale per l’esecuzione della prova Leeb. Lo studio riportato nel presente articolo è stato condotto sia su dei campioni di barre di armatura utilizzate per i controlli di accettazione, sia su barre di armatura prelevate da strutture in opera.
La durezza dell’acciaio
La durezza, hardness, è una particolare proprietà che possiede ogni materiale, non solo metallico, probabilmente quella che empiricamente è più semplice da osservare: un materiale è tanto più duro quanto maggiore è la sua capacità di resistere ad una sollecitazione di pressione localizzata. Sempre dal punto di vista empirico, ma con applicazioni dal punto di vista pratico, un materiale è più duro di un altro se questo è in grado di scalfirlo.
Rimanendo nell’ambito dei materiali metallici una tipica applicazione della durezza è quella che si fa con gli utensili da tornio: l’utensile, cioè la particolare appendice fissa o mobile che modella il pezzo di metallo, deve possedere una durezza superiore a quella del materiale lavorato.
Il problema della misura di questa particolare caratteristica meccanica dei materiali metallici si è posto nel momento in cui è iniziata la produzione industriale dell’acciaio e la relativa lavorazione. Tuttavia risalgono alla prima metà del novecento i metodi di misura della durezza dei metalli ancora oggi utilizzati: nel 1900 J. A. Brinell sviluppò una prova di compressione dei materiali metallici con una sfera che sarebbe poi diventata il metodo Brinell, nel 1920 S. R. Rockwell per testare le sue navi sviluppò il metodo di pre-forza che prese il suo nome, nel 1925 R. Smith e G. Sandland inventarono il metodo Vickers, nel 1939 F. Knoop, C. G. Peters e W. B. E. Emerson in seno al National Bureau of Standards (USA) svilupparono il metodo Knoop.
La ricerca di un metodo per misurare tale proprietà meccanica negli acciai, eseguita in maniera indipendente da diversi ingegneri, ha portato alla messa a punto di metodologie pratiche e funzionali ma non standardizzate ne associate ai sistemi metrici di riferimento, generando così diverse scale di durezza ognuna legata al metodo di prova ed al relativo strumento. La standardizzazione dei durometri e delle scale ed il relativo sforzo di creare un legame oggettivo tra le scade di durezza ed il Sistema Internazionale ha impegnato non poco negli anni gli organismi internazionali di normazione. Altro sforzo è stato poi quello di mettere a punto delle tabelle di conversione di un valore di durezza ad un altro; insomma la misura del- la durezza, ancora oggi presenta un approccio non proprio semplice per i materiali metallici: in relazione alla finalità di misura della durezza si può ricorrere a diverse metodologie la cui scelta a volte non è proprio univoca.
Ma perché misurare la durezza?
Con la misura di questa caratteristica meccanica, le cui prove presentano il vantaggio di essere semplici e rapide nell’esecuzione, economiche e soprattutto non distruttive, è possibile sia stimare le caratteristiche di resistenza di un metallo sia controllarne la qualità, in particolare nei casi in cui bisogna verificare l’efficienza del trattamento di indurimento di un metallo o misurarne l’usura.
Nei metalli la durezza è legata ai fenomeni di scorrimento plastico indotti nel materiale dalla compressione localizzata: in particolar modo negli acciai tale proprietà meccanica, assieme alla resistenza, a trazione e a compressione, è proporzionale alla percentuale di carbonio presente nella lega.
Esiste, fra l’altro, proprio una classificazione degli acciai in base alla loro durezza che aumenta all’aumentare del tenore di carbonio.
Tab. 1 – Classificazione degli acciai in base alla loro durezza

Principali metodi di misura della durezza
I principali metodi di misura della durezza, per acciai non austenitici (acciai con basso tenore di nichel), sono: il metodo Brinell, metodo Rockwell, il metodo Vickers, e il metodo Knoop.
Tali metodi di misura della durezza sono metodi statici basati sul sistema dell’impronta che consiste nel misurare appunto la dimensione dell’impronta prodotta da un corpo penetratore, di elevata durezza e di forma definita, contro il materiale da provare con una forza e per un tempo determinati.
Tali metodi si eseguono in laboratorio con appositi macchinari su campioni del materiale da sottoporre a prova. Nella macchina di prova una determinata forza viene impressa sul campione per mezzo di un penetratore, di forma e durezza standardizzata, per un determinato periodo di tempo: la forza impressa dal penetratore causa una deformazione plastica della zona del materiale, una impronta, nell’intorno del punto di contatto tra superficie del campione e penetratore e di tale impronta si misura la profondità di penetrazione (prova Rockwell) o la dimensione (metodi Brinell, Vickers e Knopp). Più un penetratore definito penetra in profondità la superficie di un pezzo (un campione) con una forza di prova definita, più il materiale testato è morbido.

Fig. 2 – Penetratore Rockwell
Fig. 3 – Impronte sui campioni ricavate con i metodi Brinell, Knopp e Vickers
Dal punto di vista ingegneristico è di notevole importanza la relazione empirica che sta alla base di tale deformazione di impronta, ossia la durezza (H) dell’acciaio è direttamente proporzionale al carico di snervamento dello stesso (σs) secondo una costante (k) all’incirca pari a 3:
H = k · σs
Si riporta di seguito una tabella esplicativa delle forme dei penetratori, le forze applicate, le formule per ricavarne la durezza.
Tab. 2 – Caratteristiche geometriche dei penetratori, carichi di prova e formule per la determinazione della durezza

La conversione dei valori di durezza
I metodi sopra descritti vengono scelti in base ai seguenti criteri: forma del penetratore (sfera, piramide o cono), materiale del penetratore (acciaio temprato, metallo duro o diamante), entità della forza di prova applicata al provino, tipo di analisi: misurazione della profondità di penetrazione (metodo di misura della profondità di penetrazione) o la dimensione dell’impronta (metodo ottico di misura) lasciata dal penetratore.
Esistono tuttavia delle tabelle di conversione approssimata della durezza, fra questa le tabelle della ASTM A370 che forniscono la conversione dalla durezza Rockwell C (carico di prova 150 kg e cono di diamante) in altri valori di durezza (Vickers, Brinell, Knopp), ovvero le tante tabelle riportate nella UNI EN ISO 18265.
Come si è già accennato con la misura della durezza è possibile stimare la resistenza a trazione dell’acciaio e tale problematica è stata trattata dai vari enti di normazione internazionali: sia nella ISO 18265 che nella ASTM A370, già sopra richiamate, sono riportate delle tabelle di conversione tra durezza e valore approssimato di resistenza a trazione dell’acciaio.
La prova di durezza Leeb
I metodi classici sopra illustrati, ancorché consolidati nel tempo e di indiscussa affi- dabilità, prevedono che il materiale da sottoporre a prova venga confezionato sotto forma di provino e sottoposto a prova in laboratorio mediante opportuni macchinari, oggi molto sofisticati.
Esistono dei durometri portatili basati sul principio delle classiche misure di durez- za, ma gli stessi risultano pesanti e ingombranti.
Si è pertanto sempre manifestata l’esigenza di poter eseguire misurazioni “in situ” su parti e componenti metallici di qualsiasi dimensione con strumenti portatili e senza la necessità di procedere a prelievi o sezionamenti di materiale, in pratica la necessità di poter eseguire la misurazione della durezza con una prova non distrutti- va anche su elementi metallici in opera.
Da tale esigenza sono state sperimentate e perfezionate tecniche di misurazione dinamica della durezza in seno alle quali la prova di durezza Leeb, nel passato nota anche come “Equotip test”, ha avuto fortissimi sviluppi sino alla normalizzazione del metodo prima da parte dell’americana ASTM (ASTM E-956) ed in seguito dalla tedesca DIN (DIN50156), per poi avere riconoscimento internazionale con la ISO 16859 “Metallic materials – Leeb hardness test”, recepita dal CEN e dall’UNI.
...continua lalettrua nel PDF , scaricabile in fondo all'articolo.
Il presente articolo fa parte degli ATTI DEL CONGRESSO NAZIONALE 2019 DELL’ASSOCIAZIONE MASTER
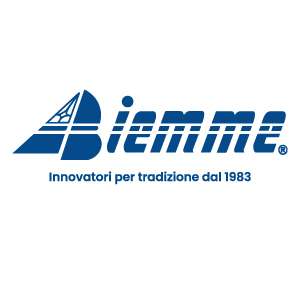
Calcestruzzo Armato
Esplora la guida completa sul calcestruzzo e sul calcestruzzo armato, due elementi fondamentali nell'edilizia. Scopri le composizioni, come l'integrazione di fibre metalliche e polimeriche, e le ultime innovazioni che migliorano le proprietà strutturali. Aggiorna le tue conoscenze sui materiali cementizi per una comprensione avanzata e applicazioni ottimali.
Controlli e Diagnostica
Una raccolta di approfondimenti per chi si occupa di fare controlli e verifiche dei materiali nel settore delle costruzioni e dell'edilizia.
Costruzioni Metalliche
Le costruzioni metalliche rappresentano una scelta strategica per strutture leggere, sicure, resistenti e sostenibili. Scopri su INGENIO tecniche, norme e soluzioni per progettare con l’acciaio.