PROGETTO TAILORCRETE: le tecnologie digitali per costruzioni complesse in calcestruzzo
L'utilizzo dei moderni software e dei sistemi di automazione per strutture complesse in calcestruzzo; il caso-studio del "Demonstrator"
L'utilizzo dei moderni software e dei sistemi di automazione per strutture complesse in calcestruzzo; il caso-studio del "Demonstrator"
È stato recentemente presentato il progetto di ricerca dell'Unione Europea denominato IG-FP7 TailorCrete sulle "Nuove tecnologie industriali per centrali di prefabbricazione su misura a prezzi compatibili con la produzione di massa" ed una sua applicazione pratica, il progetto "Demonstrator".
Avviata nell'Agosto del 2009, la ricerca ha come obiettivo la riduzione dei costi e delle tempistiche per la realizzazione di costruzioni complesse in calcestruzzo.
Attualmente i manufatti con forme complesse in calcestruzzo sono realizzati con le stesse tecniche utilizzate per gli elementi in c.c.a. standard, con conseguente aumento dei costi per la quantità di manodopera impiegata e per la dilatazione delle tempistiche; in particolare le fasi con maggiori oneri risultano essere la realizzazione e lavorazione di casseforme ed elementi di armatura.Il progetto TailorCrete, con l'ausilio di software di progettazione 3D ed innovative tecniche di produzione dei componenti e materiali in fase esecutiva, nasce con l'obiettivo di colmare questa lacuna sia nei cantieri con getto in opera, sia con sistemi strutturali prefabbricati.
Il progetto ha avuto la sua fase realizzativa nel caso del "Demonstrator", una struttura in cls gettato in opera, caratterizzata da forme molto complesse.
L'applicazione della ricerca - il progetto "Demonstrator"
Il progetto "Demonstrator", realizzato con i più moderni software di modellazione 3D, è firmato dallo studio di architettura turco Superpool. L'opera è stata realizzata ad Aarhus, in Danimarca.
La prima problematica affrontata è stata la realizzazione delle casseforme per opere non standard.
Il materiale prescelto è stato l'EPS, già ampiamente diffuso per la realizzazione di casseforme, in quanto economico, perfettamente fresabile, di peso ridotto ma al contempo dotato di forte resistenza.
L'EPS è fornito in blocchi e, se mantenuto pulito, è completamente riciclabile. Oltre alla scelta del prodotto è stato studiato un metodo per abbattere le tempistiche di produzione delle casseforme, cercando il giusto punto di equilibrio tra strategia di lavoro e qualità della superficie finale.
Nello specifico:
- i blocchi in EPS sono stati tagliati a misura con filo incandescente, considerando le casseforme anteriore e posteriore come un'unica unità, pre-tagliata con un angolo corrispondente all'andamento del manufatto in calcestruzzo.
- gli elementi pre-tagliati sono poi stati fresati nella forma definitiva utilizzando una sottostruttura per suddividerne i blocchi in una geometria non standardizzata, riducendo notevolmente il materiale di scarto.
Se il calcestruzzo gettato in opera entra in contatto con l'EPS, la fase di disarmo risulta difficoltosa, in particolare in opere, come questa, caratterizzate da forti curvature.
Nella realizzazione del "Demonstrator" è stato sviluppato un nuovo sistema dotato di una membrana in silicone, spessa 0,5 mm, applicata alla cassaforma finita. Questo metodo permette di ottenere un calcestruzzo con superficie liscia e di riutilizzare o riciclare le casseforme.
Un'ulteriore sfida affrontata nella realizzazione del "Demonstrator" è stata ottimizzare il processo di piegatura e posa delle armature, costituite in questo caso da barre di acciaio tradizionale.
Per questo tipo di operazioni, la ricerca si è concentrata sulla possibilità di automazione della produzione utilizzando tecniche digitali. In particolare, si è analizzato il potenziale dei robot industriali: questo lavoro ha portato ad una configurazione di produzione costituita da due robot. Il ROBOT 1, con compiti di caricamento, piegatura, taglio e trasporto delle barre di acciaio, ed il ROBOT 2 con compito di giunzione per la realizzazione delle reti di armatura.
Dopo queste prime fasi di produzione fuori sito si è proceduto all'avvio del cantiere; anche nella lavorazione in loco si è innanzitutto ricercata un'ottimizzazione del lavoro.Per velocizzare la fase di montaggio, le casseforme sono state numerate e, con l'ausilio del modello 3D, è stata definita con estrema precisione la posizione di ogni singolo elemento della costruzione.
Questo tipo di opera, per le sue caratteristiche, ha richiesto la predisposizione di un apposito calcestruzzo, denominato SCC. Tale miscela, autocompattante, si differenzia da quelle tradizionali per l'elevata viscosità plastica. Il prodotto è stato introdotto in opera molto lentamente per permetterne il corretto posizionamento.
Il getto in calcestruzzo è stato in gran parte realizzato con calcestruzzo SCC, tuttavia, l'ultima fase del getto, nella parte sommitale, è stata realizzata con calcestruzzo tradizionale. Non avendo controcasseri, è stata lisciata manualmente.
La realizzazione dell'opera si è dimostrata problematica nel processo di sformatura, a causa del maltempo e del posizionamento dei fissaggi della membrana, che non erano più accessibili in questa fase; se i fissaggi fossero stati posizionati sul retro delle casseforme, la sformatura sarebbe stata più agevole.
Nonostante queste problematiche, per in secondo getto di calcestruzzo, a differenza delle membrane, sostituite al 90%, è stato possibile riutilizzare tutti i blocchi in EPS.
Conclusioni:
Il progetto TailorCrete ha dimostrato che utilizzando tecnologie che esulano dalle attuali tecniche edilizie, è possibile realizzare opere in calcestruzzo, anche di notevole complessità, con:
- ottimizzazione dei costi, tramite la minimizzazione dei prodotti di scarto nella produzione delle casseforme.
- riduzione delle tempistiche e quindi dei costi sia nella fase di produzione industriale sia nella realizzazione in sito.
- possibilità di riutilizzo o riciclo dell'EPS.
- ottenimento di una superficie liscia di calcestruzzo grazie alla membrana in silicone, anche se è ancora in fase sperimentale il metodo di sformatura che individui il corretto posizionamento dei punti di fissaggio tra membrana e EPS.- la posa in opera di tutti gli elementi risulta molto facile, grazie alla produzione digitale estremamente precisa.
Le tecnologie utilizzate in questa ricerca sono innovative in ambito edile, ma già ampiamente utilizzate nell'industria di altri settori.
È quindi auspicabile utilizzare il potenziale digitale ed industriale per automatizzare i processi edilizi nelle realizzazioni in sito e nell'industria delle prefabbricazioni.
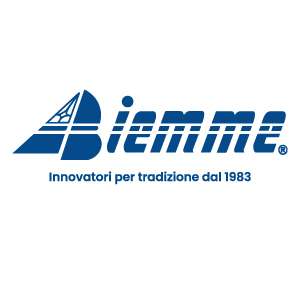
Calcestruzzo Armato
Esplora la guida completa sul calcestruzzo e sul calcestruzzo armato, due elementi fondamentali nell'edilizia. Scopri le composizioni, come l'integrazione di fibre metalliche e polimeriche, e le ultime innovazioni che migliorano le proprietà strutturali. Aggiorna le tue conoscenze sui materiali cementizi per una comprensione avanzata e applicazioni ottimali.