Pavimento in ceramica: oltre al massetto, il ruolo essenziale del sottofondo nel sistema pavimento
La durabilità di una pavimentazione in ceramica dipende dalla sinergia tra sottofondo, massetto e rivestimento. Ogni strato, se correttamente progettato, contribuisce alla stabilità e alla performance del sistema pavimento.
Sistema pavimento: nuovo modo di concepire la "stratigrafia" secondo la norma UNI 11944
Nel panorama in continua evoluzione dell'edilizia, la nuova norma UNI 11944 ha finalmente introdotto il concetto di sistema pavimento, ampliando la visione della stratigrafia del pavimento per comprendere non solo il rivestimento e il massetto, ma anche tutti gli strati sottostanti, tra cui il fondamentale sottofondo.
Questo passaggio è di particolare importanza, poiché evidenzia il ruolo essenziale che il sottofondo gioca nel garantire la stabilità, la durabilità e la performance complessiva del pavimento.
Proviamo, nel seguente articolo, a individuare come il sottofondo impatti nella posa di un pavimento in ceramica.
Sottofondo e massetto per pavimenti: due strati diversi, due funzioni distinte
Il massetto è uno strato, assimilabile ad una piastra, atto a ricevere la posa del rivestimento. Il massetto può essere di diversa natura in base al legante utilizzato (cementizio o anidritico).
Il sottofondo, a torto spesso confuso con il massetto, è uno strato diverso collocato tra l’elemento strutturale (solaio) e la stratigrafia sovrastante che ha la funzione di:
- sorreggere strutturalmente quanto sta sopra in modo stabile;
- isolare termicamente ed acusticamente (se progettato in tal senso);
- livellare il solaio alla quota di progetto;
- ospitare impianti;
- prevenire umidità di risalita (se progettato in tal senso);
- distribuire il peso del massetto e del pavimento alleggerendo così la struttura;
- fungere anche da massetto (in tal caso si parla di sottofondo bistrato);
- alleggerire la struttura.
Per approfondire, leggi anche:
Il sottofondo nel sistema pavimento: componente fondamentale dell'intera stratigrafia
I sottofondi costituiscono la componente volumetricamente predominante nella stratigrafia di una pavimentazione. In questo articolo vengono illustrate e approfondite le geometrie richieste - ovvero quota e planarità - e le tecniche necessarie per realizzarle correttamente in cantiere.
Tipologie di sottofondi per pavimenti
Tra le diverse tipologie di sottofondi possiamo trovare:
- Sottofondo in sabbia e cemento: utilizzato per raggiungere rapidamente la quota di progetto e procedere alla posa del pavimento vero e proprio;
- Sottofondo alleggerito: questa soluzione, con perle di polistirene espanso vergini e con ottimo isolamento termoacustico, è ideale per quei pavimenti nei quali verrà inserito il sistema di riscaldamento degli stessi. Esistono diverse varianti di sottofondo alleggerito con l’aggiunta di diversi materiali, oltre l’EPS vergine, come sughero, perlite, che valorizzano alcune caratteristiche tecniche, tra le quali la stabilità dimensionale anche nel tempo, permeabilità al vapore acqueo, durabilità, conducibilità termica certa, comportamento al fuoco, deformazione sotto carico e altro ancora;
- Sottofondo autolivellante o cemento cellulare: come dice la parola, possiede la tendenza a distribuirsi equamente al livello desiderato;
- Sottofondo isolante: progettato specificamente per migliorare l’isolamento termico e acustico dell’edificio;
- Sottofondo industriale: è realizzato in calcestruzzo ed è indicato per i pavimenti dei capannoni industriali e dei piazzali;
- Sottofondo a secco: realizzato senza l'impiego di leganti o acqua, può essere composto da diversi materiali, inclusi elementi come le lastre di ripartizione del carico. È una soluzione particolarmente adatta alle case prefabbricate in legno e trova largo impiego anche negli interventi di ristrutturazione su edifici storici, dove leggerezza e reversibilità sono spesso requisiti fondamentali.
Le caratteristiche di un sottofondo secondo la norma UNI 11944
La nuova UNI 11944, e in particolare il punto 5.2, stabilisce le caratteristiche imprescindibili per un sottofondo di qualità, indicando parametri come la planarità, la massa volumica, la rigidità, la deformabilità e, non da ultimo, il contenuto di umidità residua.
Quest'ultimo aspetto è di cruciale importanza, poiché l'umidità eccessiva nel sottofondo può causare danni irreversibili nel tempo, come il ritiro igrometrico che porta a fessurazioni e abbassamenti di spessore. Le problematiche legate all'umidità sono quindi uno dei fattori principali da monitorare per evitare danni strutturali.
La gestione dell'umidità in ogni strato del pavimento è essenziale per evitare danni futuri. Non si tratta solo di un problema relativo al massetto, ma dell'intero sistema pavimento, che deve essere progettato per garantire un'adeguata asciugatura e la corretta stabilità dimensionale nel tempo. Un'attenzione particolare deve essere prestata all'uso di materiali che abbiano una bassa capacità di assorbire acqua, siano a cellula chiusa, come quelli a bassa porosità, per evitare che l'umidità residua comprometta la performance del pavimento.
Resistenza a compressione e flessione di una piastrella in gres porcellanato
Oggi il gres porcellanato è il rivestimento più utilizzato per la realizzazione di pavimentazioni in ceramica. Di seguito vengono fornite alcune informazioni relative alla resistenza a compressione e flessione di una piastrella in gres, utili per comprendere le caratteristiche che un sottofondo deve possedere per essere compatibile con le prestazioni di una pavimentazione realizzata con questo materiale.
RESISTENZA A COMPRESSIONE
Cos'è la resistenza a compressione di un materiale? La resistenza a compressione misura la capacità di un materiale di resistere a forze che tendono a ridurne il volume. I materiali fragili (come la ceramica e alcuni tipi di calcestruzzo) tendono ad avere una resistenza a compressione molto superiore rispetto alla loro resistenza a trazione.
Una piastrella in gres porcellanato ha una resistenza a compressione di 3.500 kg/cm2 mentre un buon fondo di cemento arriva a 450 Kg/cm2.
Da questi valori si comprende quindi che la resistenza a compressione deve essere demandata a tutto ciò che sta sotto la piastrella e si deve parlare di resistenza a compressione del sistema pavimento.
In pratica, il massetto e il sottofondo devono essere progettati in funzione dei carichi a compressione previsti, soprattutto se puntuali che implicano elevate pressioni specifiche.
RESISTENZA A FLESSIONE
Come si misura la resistenza a flessione di una piastrella? La prova secondo norma ISO 10545-4 viene normalmente eseguita posizionando il provino (piastrella) su due supporti e applicando un carico al centro fino alla rottura. Questo metodo consente di determinare il modulo di Young e stimare la resistenza a rottura, in particolare per materiali a comportamento fragile come la ceramica. Il test fornisce due valori principali:
- Modulo di rottura: σ=3FL/2bh2
- Sforzo di rottura: S=FL/b
F = carico
L = distanza fra gli appoggi
b = dimensione provino
h = spessore piastrella
Secondo norma EN 14411 la resistenza a flessione delle piastrelle in gres porcellanato deve essere conforma ai seguenti valori:
- PIASTRELLE DI SPESSORE ≥ 7,5 mm che devono avere un carico di rottura non inferiore a 1300 N
- PIASTRELLE DI SPESSORE ≤ 7,5 mm che devono avere un carico di rottura non inferiore a 700 N
Il gres porcellanato, come tutti i tipi di ceramiche delle classi previste dalla norma EN 14411 o ISO 13006, deve quindi lavorare a flessione nei limiti sopra esposti per cui il massetto deve avere una resistenza a flessione adeguata alle condizioni d’uso della pavimentazione (come previsto dalla norma Uni 11493 e alla UNI 11944).
Di conseguenza anche il sottofondo deve collaborare a questa necessità e dovrà essere scelto in base alle condizioni d’uso della pavimentazione come allo spessore del massetto.
Una corretta progettazione deve far sì che uno sforzo a compressione sul massetto si trasformi in sforzo a flessione per la ceramica. Uno schiacciamento da compressione sul pavimento, dovuto ad esempio da un carico puntuale, può trasformarsi in un carico critico per una ceramica.
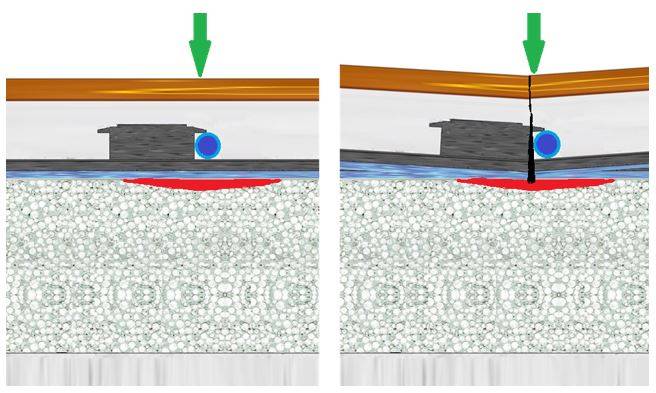
Per avere un riferimento del carico gravante sul sottofondo, al netto dei carichi di esercizio esterni e quindi dovuto esclusivamente a piastrelle e massetto, è utile considerare i seguenti valori di carico a flessione dei materiali.
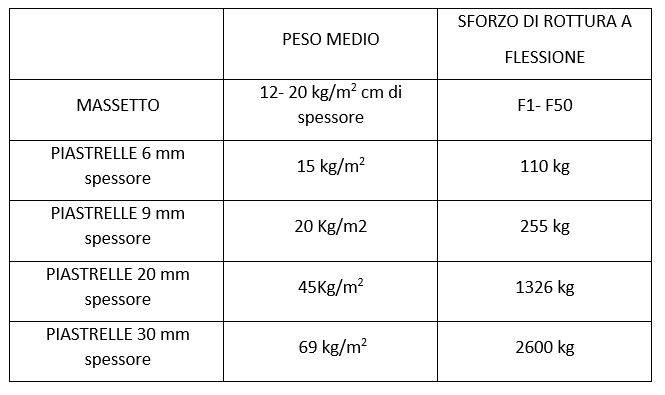
Di conseguenza, dove le condizioni d’uso sono critiche, sono da preferire spessori più elevati compatibilmente con pesi della piastrellatura più elevati.
Se una piastrella in ceramica è posata correttamente con uno strato di adesivo continuo su tutta la superficie, vale a dire in strato compatto, essa collabora con il massetto e con il sottofondo diventando un corpo unico, addirittura spessori sottili e grandi formati hanno una certa capacità di flettere prima di rompersi come dimostrato dalle lastre sottili con applicazione di stuoia in vetroresina.
Se il massetto e il sottofondo sono progettati correttamente e sono sufficientemente rigidi nei confronti delle sollecitazioni a flessione, possiamo pensare ad uno sforzo sulla piastrella prevalentemente a compressione che, come abbiamo visto ha valori elevati di resistenza a questo tipo di sollecitazione. In caso contrario, ovvero in presenza di vuoti o di un’adesione non uniforme, la piastrella viene sollecitata a flessione, risultando particolarmente vulnerabile in presenza di carichi concentrati, sia statici che dinamici.
Una corretta progettazione ma anche una corretta posa di massetto e sottofondo sono quindi doverosi. La norma UNI 11493 prevede infatti, per certe condizioni d’uso e per grandi formati, la prescrizione del letto pieno di adesivo.
Umidità nel sistema pavimento: alcune considerazioni
Come già accennato, è fondamentale prestare particolare attenzione all’impiego di materiali con bassa capacità di assorbimento e ritenzione dell’acqua durante le fasi di maturazione e asciugatura, preferendo soluzioni a bassa porosità.
Questo accorgimento è essenziale per evitare che l’umidità residua comprometta le prestazioni finali del pavimento.
La maggior parte delle piastrelle da pavimento attualmente in uso è costituita da gres porcellanato, un materiale caratterizzato da un assorbimento d’acqua inferiore allo 0,5%, che lo rende praticamente impermeabile. I gres porcellanati di alta qualità presentano valori di assorbimento ancora più bassi, spesso inferiori allo 0,1%.
Le piastrelle in gres porcellanato sono generalmente squadrate e quindi estremamente precise dal punto di vista dimensionale; per questo motivo, la posa avviene con fughe molto ridotte di soli 2 mm, e in alcuni casi addirittura senza fuga, con piastrelle completamente accostate. A questo si aggiunge la tendenza all’utilizzo di formati di grandi dimensioni – vere e proprie lastre – che, nel loro insieme, generano una superficie quasi continua e totalmente "impermeabile". In questo contesto, l’acqua eventualmente presente nel massetto incontra maggiori difficoltà a evaporare, aumentando il rischio di distacchi, problemi di adesione o accumulo di umidità residua.
L’evaporazione dell’umidità residua in eccesso può inoltre trascinare in superficie impurità presenti nel massetto, che tendono a fuoriuscire attraverso le fughe della pavimentazione, generando difetti estetici. Tra i più comuni, il cambio di colorazione del cemento delle fughe rappresenta una delle principali cause di reclamo da parte dell’utilizzatore finale.
La presenza di una barriera al vapore può impedire la corretta dispersione dell’umidità, favorendone l’accumulo lungo le pareti, con possibili danni estetici e il rischio di formazione di muffe nocive.
Infine, l’eccessiva umidità può essere un catalizzatore per la formazione di fasi espansive nel massetto con conseguenti deformazioni.
UMIDITA' RESIDUA DEL MASSETTO PER LA POSA DELLA CERAMICA
La norma UNI 11493 prescrive per i massetti cementizi un’umidità residua del 3% per i massetti di classe CT a base cemento secondo la UNI EN 13813. Questo valore è assolutamente da rispettare nel caso di massetti con riscaldamento a pavimento.
In conclusione, ogni strato del pavimento ha un ruolo specifico che contribuisce alla performance complessiva del sistema pavimento.
Il sottofondo deve essere compatibile con il massetto e il rivestimento, ma soprattutto deve garantire una solida base su cui costruire gli altri strati, rispettando le normative di resistenza e umidità. È fondamentale che i materiali scelti siano in grado di sostenere carichi elevati e resistere a sollecitazioni meccaniche, mantenendo al contempo una stabilità dimensionale che prevenga cedimenti o deformazioni nel tempo.
Il sistema pavimento deve quindi essere progettato come un insieme armonico e ben integrato, in cui ogni strato contribuisce in modo sinergico al risultato finale.
La scelta di sottofondi leggeri, resistenti e in grado di limitare l’umidità residua - come quelli a base di polistirene espanso vergine - rappresenta una soluzione innovativa per realizzare pavimenti performanti e duraturi, in piena conformità con i criteri della norma UNI 11944.
Condividi su: Facebook LinkedIn Twitter WhatsApp