Materiali, sistemi, tecniche e cantieristica negli interventi di ripristino
Gli interventi di ripristino del calcestruzzo armato richiedono un’analisi approfondita di cause, materiali e tecniche esecutive. In questo articolo, Elena Crotti, ingegnere PhD e cultore della materia, e Luigi Coppola del Dipartimento di Ingegneria e Scienze Applicate dell’Università degli studi di Bergamo illustrano in modo chiaro e dettagliato le modalità operative previste dalla norma EN 1504-9 per garantire interventi durevoli e sicuri.
1. Introduzione
La progettazione di un intervento di conservazione o di riparazione di una struttura in calcestruzzo armato non può prescindere dalla disamina delle cause responsabili delle patologie di cui l’opera è affetta.
Unitamente a quest’aspetto fondamentale, al fine di meglio comprendere e valutare i problemi connessi con l’intervento di manutenzione straordinaria è, altresì, necessario comprendere gli aspetti storico-culturali, oltre ad individuarne l’apparecchiatura costruttiva dal punto di vista sia statico che architettonico.
Infine, prima di procedere alla definizione dell’intervento di ripristino occorrerà tener conto anche delle aspettative della committenza e il contesto in cui l’opera è inserita, unitamente alle forme di gestione ed uso.
Solo nel momento in cui il progettista avrà ben chiari questi aspetti potrà procedere alla progettazione dell’intervento di ripristino indicando le strategie di intervento (i principi indicati dalla norma UNI EN 1504-9) definendo, successivamente, la scelta dei materiali e dei sistemi da impiegare per la loro attuazione, le tecniche di realizzazione, l’organizzazione del cantiere anche dal punto di vista della sicurezza.
Il progetto dell’intervento di ripristino verrà, quindi, completato da un piano che definisca le modalità di controllo e di monitoraggio nel tempo dei lavori effettuati.
La norma UNI EN 1504-9:2009
La norma UNI EN 1504-9:2009, entrata in vigore il 15 gennaio 2009, rappresenta la versione ufficiale della norma europea EN 1504-9 (edizione settembre 2008). Essa stabilisce le considerazioni di base per la specifica della protezione e della riparazione di strutture in calcestruzzo semplice e armato, utilizzando prodotti e sistemi definiti nelle norme della serie EN 1504.
Questa norma identifica undici principi fondamentali, suddivisi in due categorie principali:
• Difetti del calcestruzzo: protezione contro l’ingresso, controllo dell’umidità, ripristino del calcestruzzo, rafforzamento strutturale, aumento della resistenza fisica e resistenza ai prodotti chimici.
• Corrosione dell’armatura: conservazione o ripristino della passività, aumento della resistività, controllo catodico, protezione catodica e controllo delle aree anodiche.
Ogni principio è associato a specifici metodi di intervento, guidando i professionisti nella scelta delle soluzioni più adeguate per garantire la durabilità e l’integrità delle strutture in calcestruzzo.
2. Interventi di ricostruzione corticali
L’intervento di ripristino spesso si basa sulla preventiva ricostruzione della sezione originaria dell’elemento degradato.
Questa operazione di ricostruzione viene effettuata mediante una sequenza di operazioni che verranno nel seguito dettagliate e che in sintesi consistono, in primis, nel circoscrivere la zona interessata dal danneggiamento. Ovviamente, questa operazione non viene effettuata se il danneggiamento interessa l’intera superficie dell’elemento strutturale o quando l’estensione del danneggiamento rispetto all’area totale della struttura da riparare è così rilevante da rendere antieconomico un intervento di riparazione effettuato in maniera localizzata.
Dopo aver circoscritto l’area interessata dalla ricostruzione, si procede alla demolizione del calcestruzzo ammalorato mediante scarifica con l’ulteriore obiettivo di creare una superficie rugosa. Successivamente si procederà ad effettuare la pulizia dei ferri interessati da fenomeni di corrosione al fine di rimuovere tutta la ruggine incoerente presente sulle barre. Quindi, si procederà all’applicazione della malta da ripristino non prima di aver bagnato a rifiuto il calcestruzzo della struttura originaria. Quest’ultima operazione si rende necessaria per evitare che il supporto asciutto sottragga acqua alla malta da ricostruzione, compromettendo l’idratazione del legante all’interfaccia substrato/malta esponendo la riparazione effettuata ad un precoce distacco.
2.1 Delimitazione dell’area interessata dall’intervento di ripristino e scarifica del calcestruzzo ammalorato
Quando il degrado è localizzato in alcune zone della struttura, come avviene nel caso di strutture interessate dal fenomeno di corrosione delle barre, l’espulsione del calcestruzzo coinvolge spessori maggiori nella zona immediatamente al di sopra del tondino di armatura e via via decrescenti allontanandosi dal ferro. Di conseguenza, se ci limitassimo a rimuovere il solo calcestruzzo deteriorato, la porzione ricostruita presenterebbe spessori variabili.
In particolare, nelle aree più distanti dall’armatura, lo spessore del materiale di ripristino (malta) si ridurrebbe progressivamente fino ad annullarsi.
Poiché il ritiro di queste malte dipende dallo spessore di applicazione e aumenta con la riduzione dello spessore di riporto, si verificherebbe un elevato rischio di distacco nel tempo, soprattutto nelle zone in cui lo spessore è minimo, compromettendo l’efficacia dell’intervento di ricostruzione.
Pertanto, per prevenire il precoce distacco della malta da ripristino è fondamentale delimitare l’area da ricostruire e rimuovere anche il calcestruzzo integro per far si che in tutti i punti dello spessore di riporto sia pari ad almeno 10 mm.
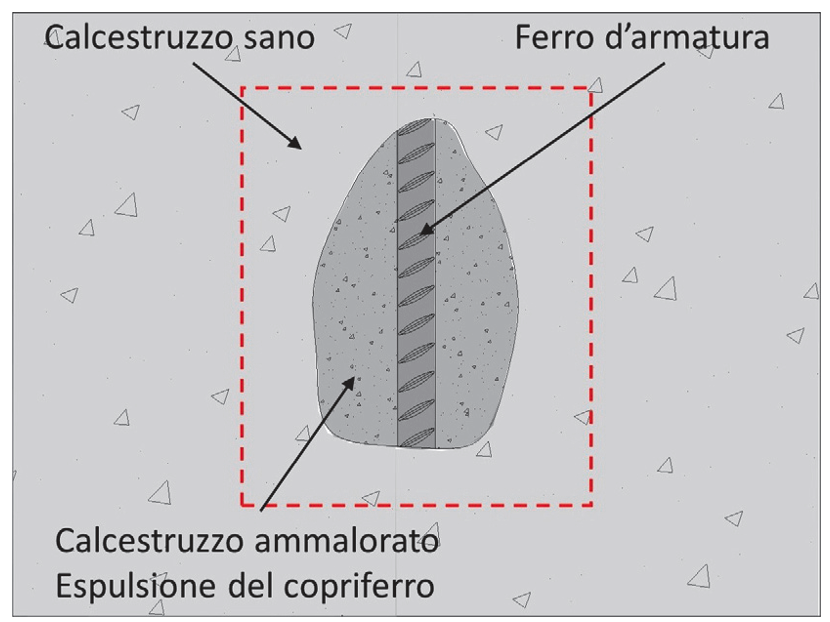
Una volta delimitata l'area da ricostruire, si potrà procedere con la scarifica del calcestruzzo utilizzando una martellina leggera nei casi di interventi localizzati (patchwork) su superfici ridotte e circoscritte o qualora si debba intervenire su aree di maggiore estensione, si opterà per l'idroscarifica o idrodemolizione.
Indipendentemente dalla tecnica utilizzata per la scarifica (martellina o idrodemolizione), l’obiettivo principale è ottenere una superficie ruvida, in grado di favorire la compenetrazione tra la malta da ripristino e il calcestruzzo esistente, migliorando così l’adesione tra i due materiali.
In genere, si consiglia di realizzare una scarifica che garantisca una superficie rugosa con asperità di circa ± 5 mm rispetto a un piano medio. La scarifica deve interessare non solo il calcestruzzo deteriorato e in fase di distacco, ma anche quello integro situato dietro le barre d’armatura. In particolare, l’operazione deve garantire la completa esposizione del ferro, rimuovendo almeno 10-15 mm di calcestruzzo nella zona retrostante il tondino.
La completa liberazione della barra di acciaio si rende necessaria per i seguenti motivi:
- Per eseguire correttamente la pulizia delle barre d’armatura e rimuovere i prodotti di corrosione anche nelle zone retrostanti al tondino, altrimenti difficili da raggiungere, è necessario garantire un’adeguata esposizione del ferro.
- Per garantire intorno al ferro un sufficiente spessore di malta da ripristino al fine di consentire una corretta trasmissione dell’aderenza acciaio/malta.
- Per favorire un maggiore contrasto del ferro all'espansione tipica delle malte premiscelate che consenta di massimizzare lo sforzo di precompressione e, quindi, di prevenire i fenomeni di fessurazione e distacco delle stesse dal supporto come conseguenza del ritiro idraulico.
- Per far si che la barra di armatura si trovi tutta annegata nella malta evitando che, a seguito di una parziale rimozione del solo calcestruzzo del copriferro, il tondino risulti annegato in parte nel vecchio calcestruzzo e in parte nella nuova malta.
2.2 Pulizia dei ferri di armatura
Completata la scarifica del substrato, è fondamentale procedere alla pulizia delle barre d’armatura.
Questa operazione può essere eseguita mediante sabbiatura, idropulizia, spazzola metallica montata su trapano e ha l’obiettivo di rimuovere i prodotti di corrosione incoerenti dalla superficie dei tondini.
Il livello di pulizia richiesto è definito dalla norma UNI EN ISO 8501-1 e deve raggiungere il grado St2 se eseguita manualmente, o Sa2.5 se effettuata con sabbiatura. Per assicurarsi che l’impresa abbia svolto correttamente la pulizia delle armature, è essenziale controllare non solo la superficie esterna visibile del tondino, ma anche la parte retrostante.
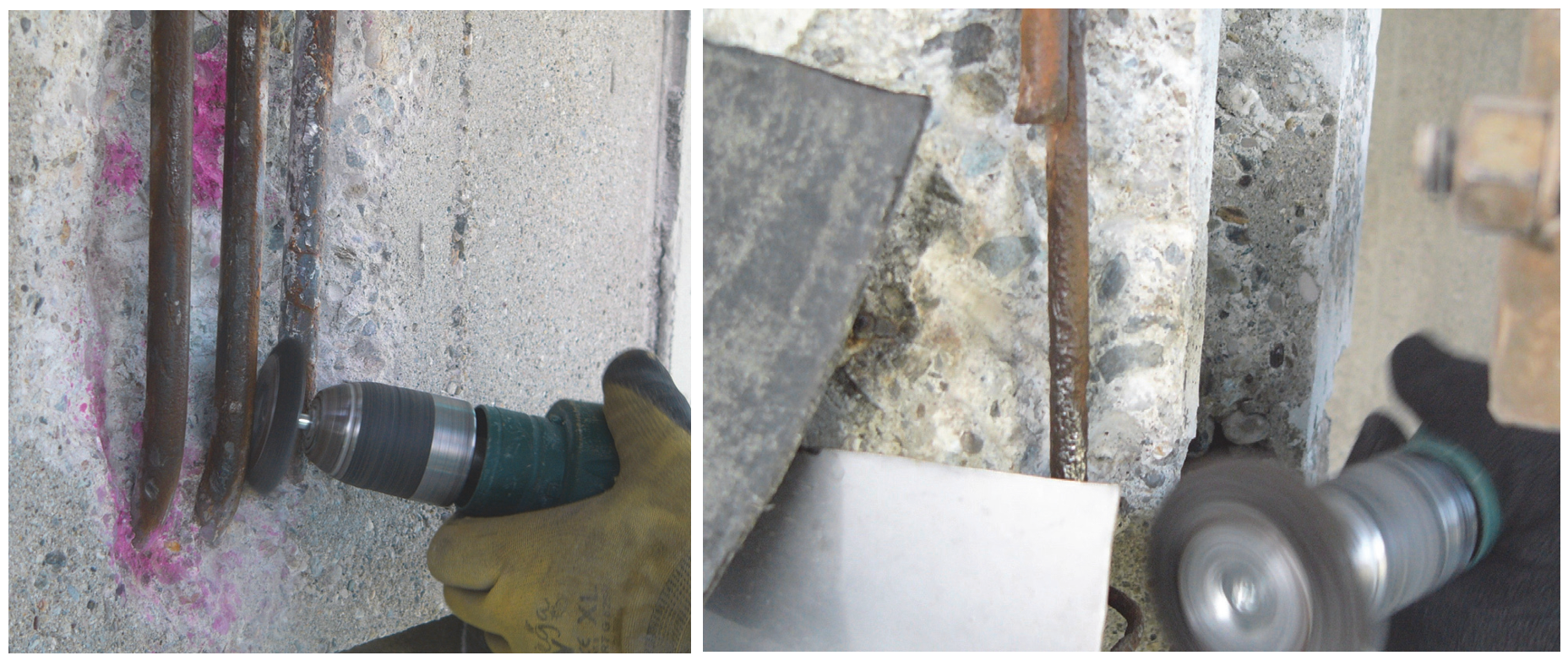
UNI EN ISO 8501-1:2012
Preparazione dei substrati di acciaio prima dell'applicazione di pitture e prodotti correlati - Valutazione visiva del grado di pulitura della superficie - Parte 1: Gradi di arrugginimento e di preparazione di substrati di acciaio non rivestito o di substrati di acciaio dopo la rimozione totale del rivestimento preesistente
Questa norma internazionale specifica una serie di gradi di ruggine e di preparazione delle superfici in acciaio non rivestite e delle superfici in acciaio dopo la rimozione totale dei rivestimenti precedenti. Fornisce descrizioni scritte accompagnate da fotografie rappresentative per ciascun grado, facilitando la valutazione visiva della pulizia delle superfici prima dell’applicazione di vernici e prodotti correlati.  
2.3 Applicazione di un protettivo per i ferri
Dopo la pulizia dei ferri è possibile applicare a pennello sul ferro un protettivo generalmente costituito da una malta polimero-cemento che deve essere conforme ai requisiti stabiliti dalla norma EN 1504-7.
Questa pratica non è strettamente necessaria qualora la preparazione del substrato sia stata eseguita correttamente, rispettando le linee guida indicate e garantendo la completa liberazione dei ferri. In tal caso, infatti, dopo la ricostruzione, il tondino risulterà completamente inglobato nella malta da ripristino, la cui elevata basicità (pH alto) ripristina le condizioni di passività del ferro.
UNI EN 1504-7:2007
Prodotti e sistemi per la protezione e la riparazione delle strutture di calcestruzzo - Definizioni, requisiti, controllo di qualità e valutazione della conformità - Parte 7: Protezione contro la corrosione delle armature
Questa norma definisce i requisiti per la protezione contro la corrosione delle armature nelle strutture in calcestruzzo. Specificando criteri per l’identificazione, le prestazioni e la sicurezza dei prodotti e sistemi utilizzati, assicura interventi efficaci nel prevenire o mitigare la corrosione, contribuendo alla durabilità e sicurezza delle strutture.
Le criticità connesse con l’applicazione del protettivo sono descritte nel seguito.
- L’operatore potrebbe essere portato a trascurare una corretta scarifica, la liberazione del ferro e la pulizia della barra, ritenendo erroneamente che lo strato protettivo possa compensare eventuali carenze nella preparazione del substrato. Tuttavia, questa convinzione è errata, poiché la barra d’armatura potrebbe presentare corrosione proprio nella parte posteriore, dove la presenza di residui corrosivi potrebbe compromettere l’adesione tra il protettivo e il tondino.
- L'applicazione del protettivo in cantiere non sempre avviene in modo ottimale e spesso si riscontrano spessori superiori a quelli raccomandati dal produttore. Questo eccesso risulta controproducente per la trasmissione degli sforzi di aderenza tra acciaio e malta, poiché riduce, ad esempio, il risalto delle barre ad aderenza migliorata.
- Per ottenere il corretto spessore del protettivo, la maggior parte dei produttori raccomanda l’applicazione in due mani, distanziate di alcune ore. Tuttavia, questa indicazione è spesso ignorata in cantiere, poiché la viscosità del prodotto permette di raggiungere lo spessore desiderato in un’unica applicazione. Di conseguenza, tale pratica compromette il corretto asciugamento del materiale, che richiederebbe più tempo per polimerizzarsi adeguatamente, se applicato secondo le istruzioni fornite nelle schede tecniche.
- Dopo l’applicazione del protettivo, è necessario attendere almeno un giorno prima di procedere alla bagnatura del substrato e alla successiva ricostruzione della sezione con malta da ripristino. Tuttavia, negli interventi di riparazione su superfici ridotte, questa prescrizione viene spesso ignorata per accelerare i tempi di esecuzione. In genere, la bagnatura del supporto e l’applicazione della malta avvengono dopo poche ore dall’applicazione del protettivo, con il rischio che quest’ultimo venga parzialmente dilavato durante la bagnatura del substrato, compromettendo così l’adesione tra acciaio e malta.
- Inoltre, durante l’applicazione del protettivo, soprattutto su ferri di piccolo diametro, non è raro che una parte del prodotto finisca accidentalmente sulla superficie del calcestruzzo. Questo strato indesiderato tende a livellare le asperità create dalla scarifica, riducendo di conseguenza l’aderenza tra la malta e il calcestruzzo.
In conclusione, qualora si scelga di utilizzare un protettivo per le armature, è fondamentale che la Direzione Lavori sensibilizzi le maestranze sulla necessità di una corretta preparazione del substrato, assicurandosi che i ferri di armatura siano completamente esposti.
Inoltre, la Direzione Lavori dovrà verificare che la pulizia delle barre sia stata eseguita fino a raggiungere il grado di finitura richiesto dal capitolato (St2 o Sa2.5) e monitorare il rispetto delle modalità applicative, dei tempi di attesa e dello spessore del protettivo, attenendosi anche alle indicazioni fornite dal produttore.
Dopo l’applicazione del protettivo superficiale, prima di procedere alla bagnatura a rifiuto del supporto e al successivo riporto di malta, è necessario attendere almeno un giorno durante i periodi caldi e 2-3 giorni in inverno, affinché il protettivo possa indurire completamente. I rivestimenti protettivi per l’acciaio devono essere conformi alla norma EN 1504-7.
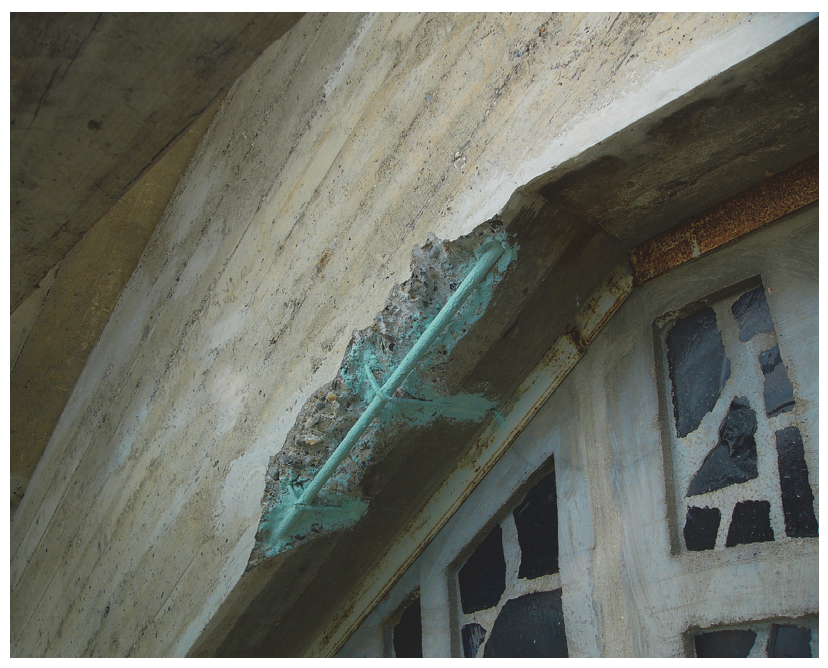
2.4 Eventuale integrazione dell’armatura e posizionamento di un’armatura di contrasto all’espansione
Negli interventi di ricostruzione generalizzati, dopo la scarifica generalizzata e dopo aver liberato completamente i ferri di armatura, si può determinare con sufficiente precisione lo spessore di malta necessario per il ripristino della sezione.
Se lo spessore di riporto sopra il ferro più superficiale è inferiore a 30-35 mm, l’irruvidimento del substrato, con asperità di circa ±5 mm, è considerato sufficiente per contrastare l’espansione della malta da ripristino. Al contrario, se lo spessore di riporto sopra il ferro più esterno supera i 35 mm, sarà necessario inserire un’armatura aggiuntiva per contrastare l’espansione della malta.
In altre parole, per spessori superiori a 35 mm, se non confinati dalla presenza di alcuna armatura, il solo effetto di adesione garantito dalle asperità della scarifica non è ritenuto sufficiente. Di conseguenza, in questi casi, si dovrà prevedere l’introduzione di un’armatura integrativa per limitare l’espansione del materiale di ripristino.
Nella Figura 4 è rappresentato schematicamente l'andamento dello sforzo di compressione, il quale risulta benefico poiché si oppone allo sforzo di trazione generato dal ritiro impedito della malta. Come evidenziato, tale sforzo raggiunge il suo valore massimo all'interfaccia con il calcestruzzo esistente, per poi annullarsi progressivamente sulla superficie della malta.
Quando lo spessore del riporto supera i 35 mm, gli strati più esterni, maggiormente soggetti al fenomeno del ritiro, risultano poco confinati e, di conseguenza, più vulnerabili alla fessurazione. Per tale motivo, è consigliabile inserire un'armatura di contrasto, in grado di generare una compressione sufficiente a prevenire la formazione di fessure negli strati superficiali.
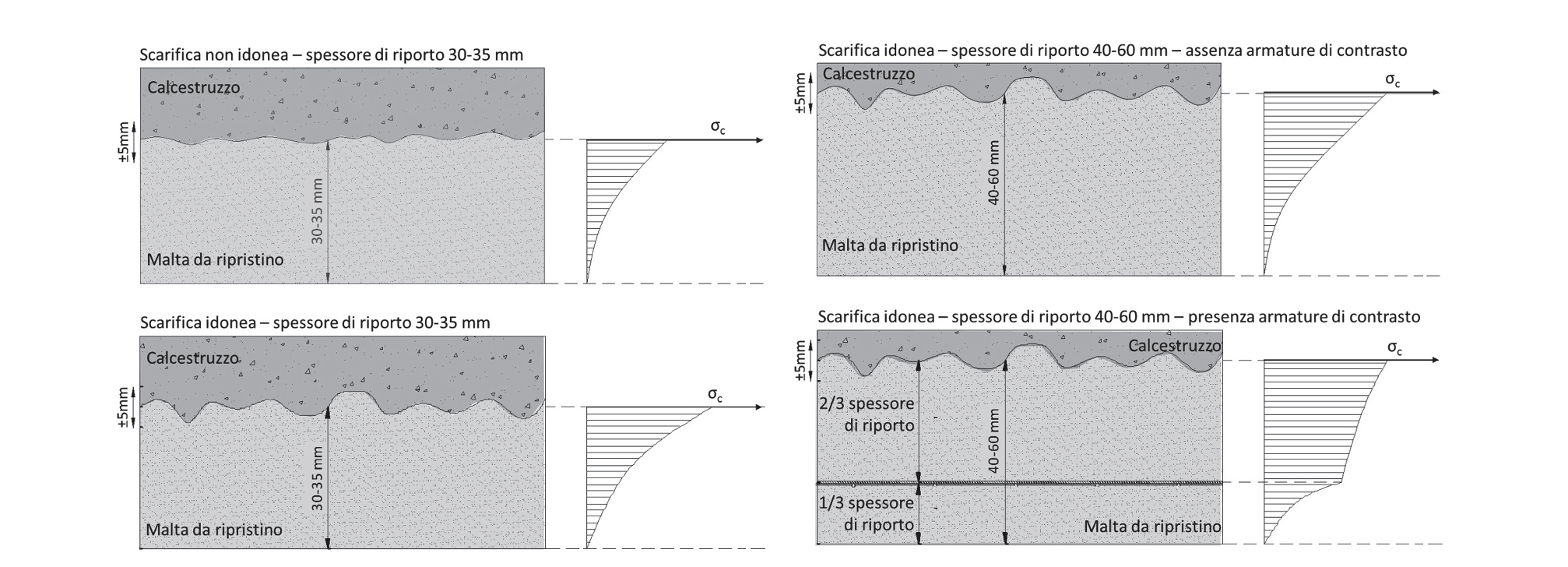
L’armatura di contrasto è realizzata con una rete elettrosaldata di piccolo diametro, compreso tra Ø3 e Ø5, con una maglia di 5 x 5 cm.
Per ottimizzarne l’efficacia, la rete viene posizionata nella zona in cui il contrasto offerto dal substrato è minimo, ovvero a un terzo dello spessore della malta non confinata dalla superficie esterna.
A tal fine, si inseriscono nella struttura in calcestruzzo dei tasselli, le cui teste devono sporgere dal substrato per una distanza pari a due terzi dello spessore della malta da applicare. Successivamente, la rete elettrosaldata viene fissata alle teste dei tasselli, che svolgono così una doppia funzione: da un lato garantiscono l’ancoraggio dell’armatura e dall’altro ne assicurano il corretto distanziamento.
Per garantire un contrasto ottimale all’espansione, la rete elettrosaldata viene posizionata a una distanza di circa 10-20 mm dalla superficie esterna. Tuttavia, questa posizione la rende potenzialmente vulnerabile alla corrosione causata dagli agenti aggressivi presenti nell’ambiente, come anidride carbonica e cloruri.
Per prevenire il degrado, la rete deve essere realizzata in:
- Acciaio zincato per le strutture aeree esposte unicamente al rischio di corrosione promosso dall’ anidride carbonica.
- Acciaio inossidabile per le strutture soggette sia all’azione della CO₂ che all’attacco dei cloruri.
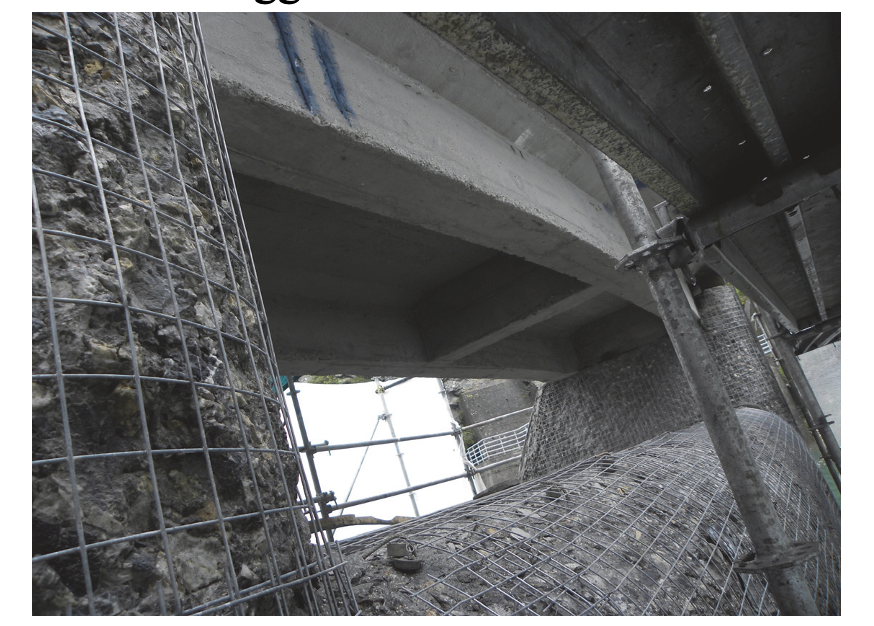
In alternativa alla rete elettrosaldata, è possibile utilizzare fibre strutturali, che possono essere metalliche oppure di natura organica (come polipropilene o poliolefine).
Per essere impiegate, le fibre devono avere la marcatura CE in conformità con la norma UNI EN 14889-1 per quelle metalliche e UNI EN 14889-2 per quelle non metalliche.
2.5 Bagnatura a rifiuto del substrato in calcestruzzo prima dell’applicazione della malta da ripristino
Dopo aver completato la pulizia delle barre di armatura (ed eventualmente applicato il rivestimento protettivo), è fondamentale saturare il supporto con acqua prima di procedere alla ricostruzione della sezione con la malta.
Questa operazione è necessaria per evitare che il calcestruzzo della struttura originaria, se non completamente saturo, assorba l'acqua presente nella malta di ripristino, compromettendo così l’idratazione del legante idraulico e, di conseguenza, l’adesione della malta al substrato. La saturazione deve essere effettuata bagnando abbondantemente la superficie e rimuovendo l'acqua in eccesso che potrebbe ristagnare in forma di rigagnoli. Questo può essere fatto utilizzando aria compressa o strofinando la superficie con stracci umidi.
In alcuni casi, prima della ricostruzione della sezione, può essere applicato un primer per riprese di getto.
Questi prodotti, a base di resine epossidiche, emulsioni acriliche o siliconati, vengono stesi sulla superficie scarificata mediante pennello, spruzzo o anche con l’uso di “innaffiatoi". In tali circostanze, la bagnatura del supporto non deve essere eseguita.
2.6 Ricostruzione della sezione dell’elemento in calcestruzzo armato con malte tissotropiche o colabili
Una volta completata la bagnatura del substrato, si procederà con la ricostruzione della sezione per ripristinare la geometria originale dell'elemento strutturale.
Nei lavori di ripristino localizzati o per scanalature, l'applicazione della malta avverrà rispettando la sezione originaria dell'elemento, anche se, una volta completata la ricostruzione, il copriferro risulti inferiore rispetto ai valori richiesti dalle normative per garantire la durabilità.
Nei casi di ricostruzione generalizzata, almeno teoricamente, sarebbe possibile aumentare lo spessore del copriferro. Tuttavia, questa soluzione è difficile da attuare nella pratica, se non in situazioni particolari e, quindi, raramente realizzata.
In ogni caso, la carenza di spessore del copriferro può essere compensata utilizzando rivestimenti protettive (da applicare sulla superficie del calcestruzzo), che, oltre a offrire protezione, possono essere colorate, consentendo così anche la decorazione delle strutture.
La ricostruzione della sezione avverrà con malte tissotropiche su elementi verticali o all’intradosso di strutture orizzontale; per contro le malte colabili verranno impiegate per gli interventi all’estradosso di strutture orizzontali.
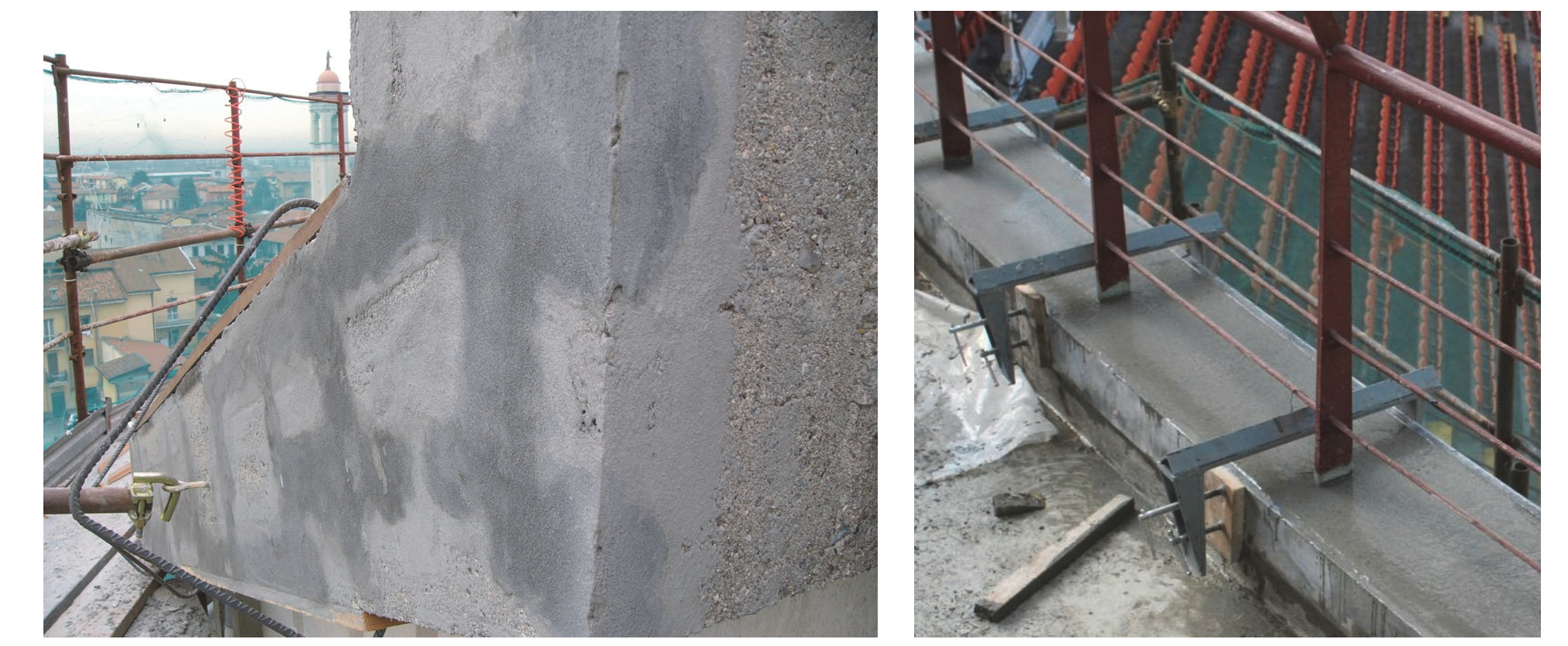
Negli interventi di ricostruzione generalizzata quando lo spessore della malta di riporto supera i 35 mm ed è stata inserita la rete di armatura di contrasto, se la ricostruzione viene eseguita con una malta tixotropica, questa deve essere applicata in due strati, ciascuno di spessore non superiore a 30-35 mm. Tale obbligo non si applica, invece, agli interventi di ricostruzione localizzata con malte tixotropiche quando il substrato è stato preparato tramite scanalature, né per le malte colabili, che devono essere applicate in un unico strato.
L'applicazione delle malte tixotropiche in doppio strato può essere effettuata in due modi:
- Con la tecnica "fresco su fresco": questa modalità consiste nell'attendere che il primo strato di malta inizi la presa prima di applicare il secondo. Di solito, l'operatore verifica questa condizione appoggiando la mano sulla superficie della malta con una leggera pressione: Se, a seguito della pressione la malta rimane attaccata alle dita, significa che non ha ancora iniziato la presa, quindi bisogna aspettare ancora prima di applicare il secondo strato;
se la superficie della malta presenta i segni della pressione dei polpastrelli e le dita rimangono pulite, ciò indica che la malta ha cominciato la presa, e quindi si può procedere con l'applicazione del secondo strato;
se sulla superficie della malta non restano i segni delle dita, significa che la malta ha completato la presa, e l'applicazione del secondo strato non potrà avvenire nella stessa giornata, ma dovrà essere rinviata al giorno successivo. - Con la tecnica “fresco su indurito”: questa modalità consiste nell’applicare il primo strato di malta e nell’attendere almeno 24 ore (ma non più di tre giorni) prima di procedere al completamento della ricostruzione della sezione con il secondo strato.
Naturalmente, quando si utilizza la tecnica “fresco su fresco”, non è necessario bagnare il primo strato prima di applicare il secondo. Per contro, nel caso in cui si adotti la tecnica “fresco su indurito”, sarà indispensabile bagnare il primo strato prima di procedere con l'applicazione del secondo.
Indipendentemente dalla scelta della tecnica, è fondamentale seguire un'altra regola pratica: la rete di contrasto deve essere completamente immersa nel secondo strato di malta.
Essa non può trovarsi:
- completamente immersa nel primo strato di malta. In questo caso, infatti, il contrasto all'espansione del secondo strato di malta sarebbe affidata alla sola adesione tra i due strati. Al contrario, il primo strato di malta beneficerebbe del contrasto esercitato sia dall'adesione al calcestruzzo originario che dalla rete di armatura;
- parzialmente immersa tra il primo e il secondo strato. In questa situazione, il secondo strato di malta, non avvolgendo completamente la rete elettrosaldata, avrebbe un contrasto limitato.
2.7 Modifica e/o omogeneizzazione della tessitura superficiale, del colore e dell’estetica degli elementi in calcestruzzo armato
Ultimata la ricostruzione della sezione si possono presentare le seguenti situazioni:
- L'intervento è stato eseguito mediante scanalature e ha interessato solo parzialmente la superficie dell'elemento in calcestruzzo armato (Figura 7). Di conseguenza, le aree ripristinate presentano una tessitura più fine e un colore più scuro rispetto alle parti originarie. Qualora sia importante ottenere una superficie con una tessitura e un colore omogeneo, è necessario applicare uno strato sottile (2-3 mm) utilizzando una malta a grana fine, preparata con premiscelati contenenti sabbie di piccolo diametro (0.5 mm). Queste malte vengono chiamate rasature. La realizzazione della rasatura, comunque, risulta superflua quando l'elemento in calcestruzzo sarà successivamente intonacato. Se l'intervento prevede una protezione o decorazione a basso spessore (solitamente inferiore a 150 micrometri) a base acrilica, sarà necessario valutare se applicare o meno la rasatura (Figura 7). Generalmente, in queste situazioni, si preferisce comunque rasare la superficie dell'elemento in c.a. per evitare che il rivestimento acrilico mostri zone con colorazioni e tessitura diverse, causate dal diverso assorbimento della pittura protettiva tra il calcestruzzo originario e le aree ripristinate con malta.

- L'intervento è stato realizzato tramite scanalature e ha coinvolto la superficie di un elemento in calcestruzzo facciavista con tavole di legno. In questo caso, dopo il ripristino, la superficie risulta non omogenea sia nella tessitura che nel colore e mostra un'interruzione nel disegno delle tavole nei punti in cui sono stati effettuati i lavori di recupero. Se è necessario ripristinare la continuità del disegno delle tavole, si procederà con la realizzazione di uno strato di rasatura dello spessore di 4-8 mm, che, mentre è ancora fresco, verrà stampato con tavole di legno che riproducono, per dimensioni e venature, quelle delle tavole originali utilizzate nella costruzione della struttura (Figura 8).

- L'intervento di ripristino è stato eseguito con malta tixotropica e ha interessato l'intera superficie di un elemento in calcestruzzo che, prima della ricostruzione, è stato sottoposto a una scarifica generalizzata. In questo caso, la superficie appare omogenea sia nella tessitura che nel colore, ma risulta piuttosto grezza (Figura 9). Se si desidera ottenere una tessitura più fine ("a civile finissimo"), sarà possibile applicare uno strato di rasatura superficiale con uno spessore di 2-3 mm.
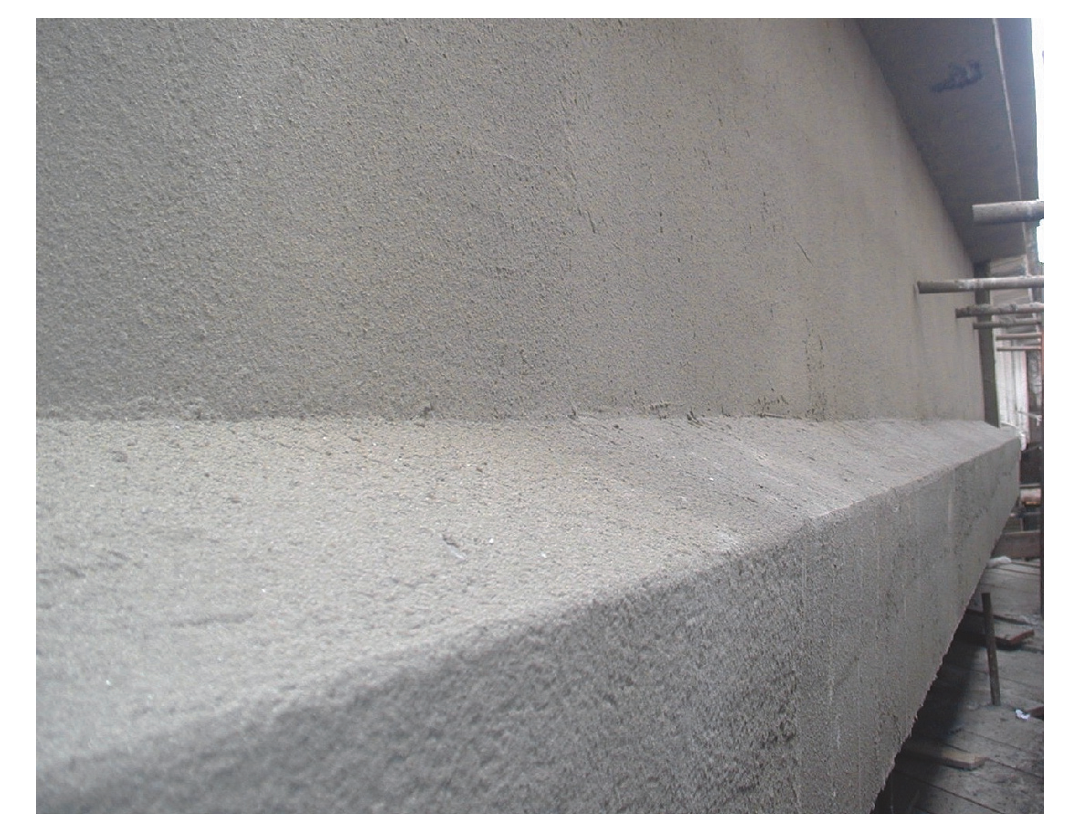
- L'intervento di ricostruzione è stato realizzato con getto di malta colabile all'interno di un cassero. In questo caso, anche se sono state utilizzate malte preparate con sabbie di pezzatura massima di 4 mm, la superficie risulta generalmente liscia e non richiede ulteriori rasature superficiali (Figura 10).

A prescindere dalle ragioni che rendono necessaria una rasatura superficiale, il sistema cementizio impiegato deve rispettare i seguenti requisiti:
- Deve avere principalmente una funzione estetica, presentando quindi una tessitura fine.
- Deve garantire compatibilità deformazionale con il supporto su cui viene applicato, evitando distacchi o la formazione di antiestetiche "sbollature".
Per quanto riguarda l’adesione della rasatura al supporto, è chiaro che questa caratteristica dipenda non solo dalla qualità del premiscelato impiegato, ma anche in maniera significativa dalle modalità di preparazione del substrato. A tale proposito, sarà necessario eseguire un’accurata pulizia della superficie in calcestruzzo esistente, utilizzando un’idropulizia a bassa pressione, in modo da rimuovere esclusivamente lo strato superficiale di cemento (“lattime”).
Se la rasatura viene applicata su uno strato di malta tixotropica a ritiro compensato, utilizzata per un intervento di ripristino generalizzato esteso all’intera superficie di un elemento in calcestruzzo, non è necessario eseguire un’idropulizia preliminare. Indipendentemente dalla tecnica adottata per la preparazione del substrato, prima di procedere con la rasatura, è necessario effettuare una bagnatura del supporto, assicurandosi poi di eliminare l’acqua in eccesso con aria compressa o panni umidi.
La rasatura deve garantire compatibilità deformazionale con il supporto.
Tuttavia, nel caso delle rasature, a causa del ridotto spessore il ritiro risulta più elevato e ,quindi, per evitare che la rasatura si fessuri o si distacchi dal supporto, è necessario minimizzare lo sforzo di trazione indotto dal ritiro impedito (𝜎ct) in modo che non superi la resistenza a trazione della rasatura (fct):
f_ct>σ_ct
Atteso che 𝜎ct è esasperato dal basso spessore dello strato, la diminuzione dello sforzo di trazione non può che essere perseguita attraverso una drastica diminuzione del modulo di elasticità della rasatura (Emr):
σ_ct=E_mr∙ε_(cs-c)
Conseguentemente, nella scelta di un premiscelato per rasatura si opererà nel seguente modo:
- Negli interventi di ricostruzione puntuale, che hanno coinvolto solo una parte della superficie dell'elemento in calcestruzzo, si dovrà impiegare una rasatura con il più basso modulo elastico disponibile. Questo significa optare per una malta con classe di resistenza R2 (malta per rasatura classificata come MR-R2) in conformità alla normativa EN 1504-3.
- Negli interventi di ricostruzione estesi, in cui l'intera superficie della struttura in calcestruzzo è stata ripristinata utilizzando una malta tixotropica (MT) la compatibilità deformazionale risulta più agevole da garantire. Questo avviene perché la differenza di contrazione dimensionale è inferiore rispetto a una rasatura applicata direttamente sulla struttura in calcestruzzo originale, in quanto entrambi i sistemi cementizi devono ancora esplicare gran parte del ritiro idraulico. Tuttavia, considerando che la rasatura, per via del suo spessore ridotto, è soggetta a un ritiro più rapido e accentuato rispetto a quello della malta applicata a spessore maggiore, si adotterà il principio di selezionare una rasatura con un modulo elastico comunque inferiore a quello del materiale cementizio impiegato per la ricostruzione.
2.8 Eventuale protezione e/o decorazione delle superfici degli elementi in calcestruzzo armato
Dopo aver completato la ricostruzione della sezione ed eventualmente applicato lo strato di rasatura si possono presentare le seguenti condizioni:
- la superficie della struttura ripristinata e rifinita con rasatura appare uniforme per tessitura e colore, ma lo spessore del copriferro risulta insufficiente a garantire la protezione dalla corrosione per il periodo previsto prima del prossimo intervento di manutenzione e/o richiede una finitura decorativa colorata;
- la superficie della struttura ricostruita con malta tixotropica e rifinita con rasatura risulta omogenea per tessitura e colore, dispone di un copriferro adeguato, ma necessita comunque di una finitura decorativa colorata;
- la superficie di strutture in calcestruzzo facciavista, sottoposta a interventi localizzati di ripristino, richiede un trattamento protettivo per la carenza di un copriferro di adeguato spessore e/o un intervento di finitura decorativa;
- la superficie di una struttura in calcestruzzo, sottoposta a un ripristino parziale o a una ricostruzione generalizzata, necessita di una protezione o impermeabilizzazione e, se necessario, di una finitura decorativa.
I rivestimenti protettivi da applicare sulla superficie di un elemento strutturale sottoposto ad intervento di ricostruzione si distinguono in accordo alla norma EN 1504-2 in: rivestimenti filmogeni (tipo C: coating), trattamenti idrofobici (tipo H: Hydrophobe) e trattamenti impregnanti (tipo I: Impregnation).
I rivestimenti filmogeni sono protezioni che creano una pellicola continua sulla superficie del calcestruzzo. Questi sistemi vengono impiegati nel campo della manutenzione e del ripristino per affrontare una delle problematiche più frequenti nelle strutture esistenti: lo spessore ridotto del copriferro. L’obiettivo principale dei rivestimenti protettivi filmogeni è quello di bloccare o rallentare la penetrazione di sostanze dannose per il calcestruzzo e per le armature metalliche, come l’anidride carbonica (CO₂) e/o i cloruri. Oltre alla funzione protettiva, questi rivestimenti vengono anche utilizzati per migliorare l’aspetto estetico delle superfici in calcestruzzo, poiché spesso sono colorati, combinando così protezione e decorazione.
Lo spessore di applicazione dei rivestimenti filmogeni a base acrilica varia tra 100 e 180 μm. Questi prodotti filmogeni a base acrilica vengono applicati dopo aver steso un primer sulla superficie del calcestruzzo. I primer utilizzati sono generalmente resine in dispersione acrilica, che vengono applicate a pennello (per superfici piccole) o a spruzzo con sistemi airless (per superfici più ampie), con l’obiettivo di uniformare le proprietà di assorbimento del materiale del supporto. La porosità e, di conseguenza, le proprietà di assorbimento del calcestruzzo originario e quelle del materiale di ripristino utilizzato per le riparazioni locali sono differenti e potrebbero causare variazioni cromatiche una volta che il protettivo si asciuga. Per evitare questo problema, si applica un primer, che ha uno spessore ridotto (circa 50 μm) e una composizione acrilica simile a quella del prodotto filmogeno applicato successivamente in due mani.
I rivestimenti acrilici generalmente non sono “elastici” e presentano una capacità limitata di crack-bridging, ossia una scarsa attitudine a coprire fessurazioni nel calcestruzzo senza subire lacerazioni. Il valore effettivo di crack-bridging, ovvero l’ampiezza della fessura che il rivestimento può coprire senza rompersi, varia generalmente tra 0,3 mm e 0,5 mm.
Questo significa che il loro potere di copertura delle lesioni è estremamente basso. Di conseguenza, i rivestimenti acrilici devono essere applicati esclusivamente su strutture in calcestruzzo prive di fessure e su elementi per i quali non si prevede la formazione di un quadro fessurativo significativo nel tempo.
Tra i sistemi protettivi troviamo anche gli idrorepellenti, questi prodotti non sono filmogeni e, di conseguenza, non chiudono le porosità superficiali, ma sono in grado di ridurre l’assorbimento di acqua da parte del calcestruzzo.
Gli idrorepellenti vengono anche impiegati come sistemi di protezione contro i graffiti, o meglio, per agevolare la pulizia delle superfici in calcestruzzo che vengono macchiate con vernici spray. Se il calcestruzzo è trattato con un prodotto idrorepellente, la vernice spray penetra con maggiore difficoltà, rimanendo solo in superficie, mentre in un calcestruzzo non trattato essa può infiltrarsi nelle porosità per alcuni millimetri rispetto alla superficie. Pertanto, se si effettua un trattamento di pulizia su un calcestruzzo non trattato e imbrattato con vernici, per rimuovere completamente la vernice si dovrebbe abradere la superficie; invece, utilizzando un prodotto idrorepellente per ridurre l’assorbimento della vernice, la pulizia risulterebbe notevolmente semplificata.
Gli idrorepellenti modificano il comportamento del materiale su cui vengono applicati, trasformando un materiale idrofilo in uno idrofobo e quindi, vengono utilizzati per trattare il calcestruzzo quando è necessario mantenere l’estetica, poiché questi prodotti non alterano l’aspetto superficiale del calcestruzzo (non vi è alcuna differenza visibile tra un calcestruzzo trattato e uno non trattato).
I prodotti idrorepellenti conferiscono al materiale su cui sono applicati un comportamento idrofobo quando entrano in contatto con acqua a bassa pressione (come la pioggia), ma non sono adatti per strutture idrauliche a contatto permanente con acqua.
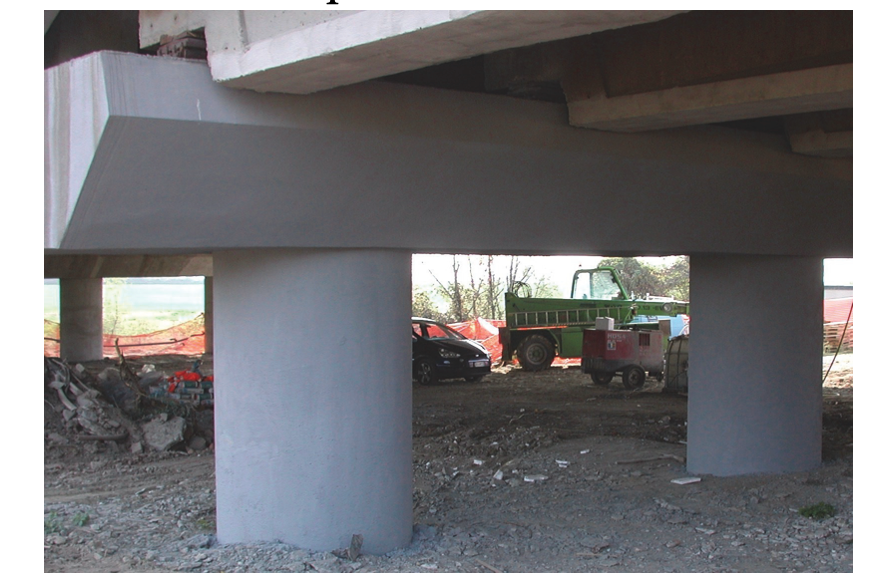
Per le strutture idrauliche, soggette a contatto continuo con l'acqua, come nel caso di canali, vasche di contenimento o strutture esposte alle soluzioni contenenti cloruri o all’acqua di mare l’uso di prodotti acrilici è da escludere, preferendo invece i sistemi polimero-cemento.
Questi ultimi, applicati con spessori di 2-3 mm, non richiedono una rasatura preliminare, necessaria invece per le resine in dispersione acrilica.
La differenza principale tra i rivestimenti acrilici e quelli in polimero-cemento (PC) risiede nella capacità di crack-bridging.
I rivestimenti polimero-cemento possiedono una maggiore capacità di coprire le fessurazioni rispetto ai prodotti acrilici, potendo sigillare lesioni anche superiori a 0.6 mm. I rivestimenti polimero-cemento, inoltre, possono essere impiegati quando è necessaria una tenuta idraulica, sia in condizioni di spinta positiva dell'acqua (come nel caso di una vasca di contenimento), sia in presenza di spinta negativa (ad esempio, su una parete interrata, dove il rivestimento viene applicato all'interno dell’ambiente mentre l'acqua esercita pressione sulla faccia esterna del muro in calcestruzzo). In genere, si considera che i rivestimenti polimero-cemento siano in grado di resistere a spinte positive fino a 3 atm e negative fino a 1 atm.
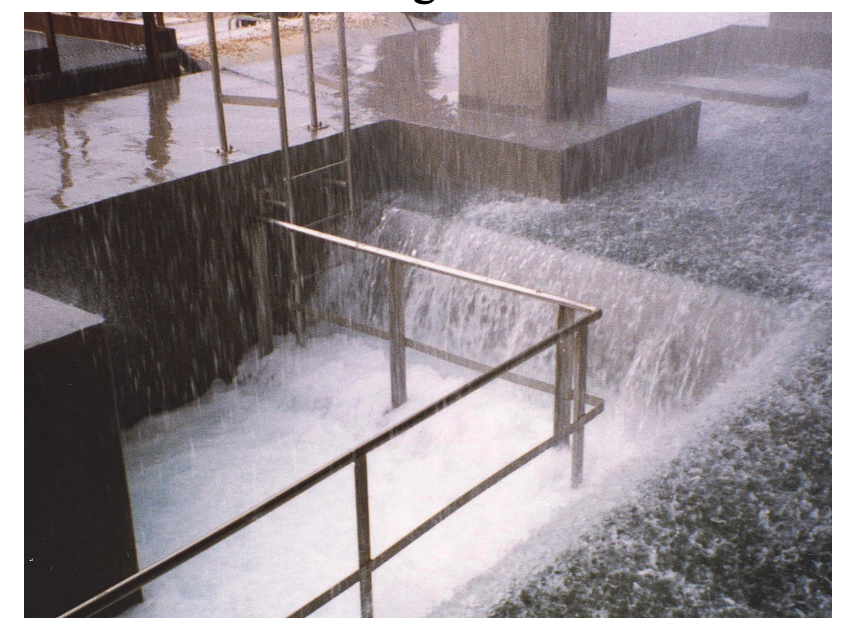
3. Conclusioni
Indipendentemente dal ciclo di riparazione che verrà adottato (solo malta, oppure malta + rasatura o malta + rasatura + protezione), l’intervento di ripristino si basa in ogni caso sulla preventiva ricostruzione della sezione originaria dell’elemento degradato.
Questa operazione di ricostruzione viene effettuata mediante una sequenza di operazioni e che in sintesi consistono nel circoscrivere la zona interessata dal danneggiamento, nella demolizione del calcestruzzo ammalorato mediante scarifica con l’ulteriore obiettivo di creare una superficie rugosa contro cui applicare il materiale da ripristino.
Successivamente si procederà ad effettuare la pulizia dei ferri interessati da fenomeni di corrosione al fine di rimuovere tutta la ruggine incoerente presente sulle barre.
Quindi si procederà all’applicazione della malta da ripristino non prima di aver bagnato a rifiuto il calcestruzzo della struttura originaria.
La ricostruzione della sezione avverrà con malte tissotropiche su elementi verticali o all’intradosso di strutture orizzontale; per contro le malte colabili verranno impiegate per gli interventi all’estradosso di strutture orizzontali. La scelta di procedere all’applicazione di una rasatura, inoltre, è dettata quasi esclusivamente da considerazione di carattere estetico.
Infine, l’intervento si completa con l’applicazione di una protezione superficiale - che può avere anche funzione decorativa – per sopperire ai ridotti spessori di copriferro tipici delle strutture realizzate in passato.
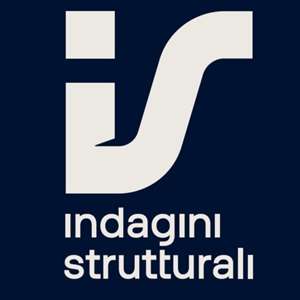
Indagini Strutturali
Con il topic "Indagini Strutturali" vengono raccolti tutti gli articoli pubblicati sul Ingenio sul tema della diagnostica strutturale e riguardanti la progettazione, l'applicazione, l'innovazione tecnica, i casi studio, i controlli e i pareri degli esperti.

Interventi strutturali
In questa area di INGENIO, una raccolta di news ed articoli di approfondimento sulla normativa, progettazione, casi applicativi e soluzioni per interventi su strutture e infrastrutture.

Malte da Restauro
Con il topic "Malte da Restauro" vengono raccolti tutti gli articoli pubblicati sul Ingenio sulle malte da restauro e riguardanti la progettazione, l'applicazione, l'innovazione tecnica, i casi studio, i controlli e i pareri degli esperti.
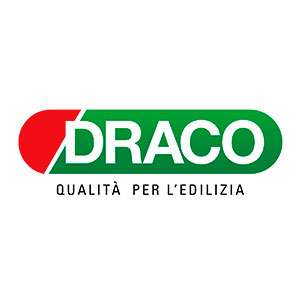
Malte da Rinforzo Strutturale
Con il topic "Malte Strutturali" vengono raccolti tutti gli articoli pubblicati sul Ingenio sulle Malte ad uso Strutturale e riguardanti la progettazione, l'applicazione, l'innovazione tecnica, i casi studio, i controlli e i pareri degli esperti.

Rinforzi Strutturali
News e approfondimenti su tutto quello che riguarda il rinforzo delle strutture: dalla modellazione e progettazione degli interventi, alla normativa, alla descrizione di soluzioni tecniche e particolari costruttivi.
Condividi su: Facebook LinkedIn Twitter WhatsApp