Le caratteristiche tecniche più importanti delle piastrelle di ceramica per ambienti pubblici
Numerose sono le caratteristiche da tenere in considerazione quando si progetta una pavimentazione in piastrelle per l'edilizia pubblica. Per ciascuna di queste, è stata preparata una scheda di approfondimento, contenente informazioni sul metodo di misura ed un'analisi critica dei requisiti specificati dalle norme, in rapporto con le caratteristiche (micro)strutturali del materiale (assorbimento d'acqua, porosità, ecc.), nell'ambito di una visione generale del quadro prestazionale.
Nella Tab. 2.II sono state identificate, sulla base della norma EN 14411, le caratteristiche che le piastrelle debbono possedere in relazione all’uso cui sono destinate.
Fra queste, quelle più significative per le destinazioni in ambienti pubblici, e dunque per assicurare una conveniente risposta alle sollecitazioni ed esigenze identificate nella Tab. 1.II (vedi articolo linkato a fondo pagina), sono le seguenti:
• Resistenza a flessione e sforzo di rottura
• Resistenza all'abrasione
• Resistenza all'attacco chimico
• Cessione di piombo e cadmio
• Resistenza allo scivolamento
Per ciascuna delle caratteristiche sopra elencate, è stata preparata una scheda di approfondimento, contenente informazioni sul metodo di misura ed un'analisi critica dei requisiti specificati dalle norme, in rapporto con le caratteristiche (micro)strutturali del materiale (assorbimento d'acqua, porosità, ecc.), nell'ambito di una visione generale del quadro prestazionale.
Le caratteristiche possedute da un prodotto o un tipo di piastrella di ceramica, così come la sua conformità ai requisiti normativi, possono essere semplicemente dichiarate dal produttore, sulla base delle misure autonomamente effettuate, o certificata da una terza parte indipendente. I marchi di qualità - richiamati sotto - sono strumenti molto utili ed utilizzati dai produttori italiani di piastrelle di ceramica.
I Marchi di Qualità
Il laboratorio ufficiale italiano per il controllo della rispondenza delle caratteristiche del prodotto con i requisiti delle norme o con quanto promesso dal produttore è il Centro Ceramico di Bologna.
La conformità delle piastrelle con quanto prescritto dalle norme può essere semplicemente dichiarata dal produttore, con riferimento alla consegna effettuata, o certificata da un ente apposito il quale, sulla base del controllo del prodotto e della verifica dell'affidabilità della gestione del processo produttivo, concede al prodotto stesso un Marchio di Qualità, che viene poi riportato sia sul catalogo, sia sulle singole confezioni del prodotto.
Resistenza a flessione e sforzo di rottura a flessione
Definizione/descrizione: La resistenza alla flessione, o modulo di rottura a flessione , è un parametro caratteristico di ogni materiale, e corrisponde alla massima tensione che un provino del materiale stesso, sottoposto ad una crescente sollecitazione di flessione in condizioni e con procedure definite, può sopportare prima di rompersi. L’unità di misura è N/mm2.
La resistenza a flessione è una caratteristica del materiale che costituisce la piastrella, e non definisce direttamente alcuna prestazione meccanica della piastrella stessa. Essa viene controllata per verificare la correttezza del processo produttivo adottato, in relazione al raggiungimento del voluto grado di consistenza e compattazione.Il carico di rottura a flessione è il carico che, applicato in condizioni e con modalità definite, porta alla rottura della piastrella sottoposta a prova. Lo sforzo di rottura si ottiene moltiplicando il carico di rottura per il rapporto L/b (si veda la Fig.3.1 per il significato di tale rapporto). L’unità di misura, sia per il carico che per lo sforzo di rottura, è il N.
Il carico e lo sforzo di rottura, per loro stessa definizione, rappresentano una caratteristica prestazionale della piastrella, determinata sia dalle caratteristiche strutturali del materiale costituente, sia dalle dimensioni della piastrella stessa. Il carico di rottura tende ad aumentare, in particolare, all'aumentare del modulo di rottura del materiale e dello spessore della piastrella.
Metodo di misura: EN ISO 10545 Parte 4: il provino - la piastrella - viene collocato su due rulli, ed un carico crescente viene applicato in mezzeria per mezzo di un terzo rullo (Fig. 3.1). Il carico viene applicato in modo uniforme e con incremento costante (1 N/mm2s), fino alla rottura della piastrella. Si registra il carico di rottura F, e si calcolano il modulo di rottura s e lo sforzo di rottura S con le formule:
σ= 3FL/2bh2
S = FL/b
Il significato dei simboli è riportato in Fig. 3.1Correlazioni con altre proprietà: Il modulo di rottura σ, caratteristica del materiale costituente la piastrella, tende ad aumentare all'aumentare della compattezza, ovvero al diminuire della porosità. Possiamo trovarne conferma nel diagramma di Fig. 3.2, che riporta l'andamento del modulo di rottura in funzione dell'assorbimento d'acqua, per un consistente campione di piastrelle ottenute per pressatura.
Come dimostrato dalla formula sopra riportata, il carico di rottura, misura della “prestazione meccanica” della piastrella, aumenta all'aumentare sia del modulo di rottura, sia dello spessore. Giova però sottolineare che l'influenza dello spessore sul carico di rottura è maggiore, in quanto lo spessore compare con esponente 2. Ne deriva che mentre, ad esempio, ad un raddoppio del modulo di rottura corrisponde
un raddoppio del carico di rottura, un raddoppio dello spessore porta, a parità di ogni altra condizione, ad un carico di rottura incrementato di quattro volte.
Requisiti: I requisiti per il modulo di rottura e lo sforzo di rottura sono, come prevedibile, decrescenti all'aumentare dell'assorbimento d'acqua (dunque passando dai Gruppi I ai Gruppi III, come documentato in Tab. 3.I.)
Discussione: In ambienti - in particolare, in pavimenti - nei quali sono previste condizioni di esercizio con sollecitazioni meccaniche massive molto gravose, la scelta dovrebbe prudentemente orientarsi su piastrelle dei gruppi I o IIa (ad esempio, BIa, BIb, AI, AIIa), con una forte attenzione allo spessore delle piastrelle. In questo caso però l'influenza della piastrella sulla resistenza meccanica e sulla durabilità della pavimentazione non deve essere sopravvalutata: non bisogna infatti dimenticare che il carico di rottura della singola piastrella, misurato secondo le modalità previste dalla norma EN ISO 10545 Parte 4, è generalmente assai inferiore alla reale capacità di carico della medesima piastrella in esercizio, allorché essa è inserita nel pavimento. Si può dimostrare, mediante calcoli e modelli matematici, che la capacità di carico della piastrella posata è superiore, spesso di alcune decine di volte, al carico che provoca la rottura, durante la prova di resistenza alla flessione in laboratorio, della piastrella singola svincolata dal piano di posa. Questa conclusione è per altro intuitiva, sol che si tenga conto della determinante collaborazione alla resistenza alle sollecitazioni meccaniche, che la piastrella riceve dagli strati (l'allettamento, il supporto) ad essa stabilmente collegati. Un ulteriore suggerimento: in pavimenti particolarmente sollecitati appare maggiormente prudente la scelta di formati non eccessivamente grandi. Ad un formato piccolo delle piastrelle corrisponde una minore rigidità della piastrellatura, e quindi una limitazione dello stato tensionale interno associato alle sollecitazioni di esercizio.
Resistenza all’abrasione
Definizione/descrizione: La resistenza all'abrasione rappresenta la resistenza che la superficie oppone alle azioni di usura connesse con il movimento di corpi, superfici o materiali a contatto con essa.
Gli effetti delle azioni abrasive possono essere di due tipi:
• l'asportazione di materiale dalla superficie, che quindi viene progressivamente consumata;
• l'alterazione delle caratteristiche estetiche della superficie stessa, con perdita di brillantezza, variazione di tonalità cromatica, ecc.
Si tratta di effetti diversi, non sempre concomitanti e spesso neppure correlabili: nel senso che, ad esempio, una notevole asportazione di materiale in superficie non sempre e non necessariamente si accompagna ad un grave deterioramento estetico, e viceversa. Giova tuttavia sottolineare un aspetto molto importante: indipendentemente dagli effetti estetici immediati, in generale la rimozione di materiale ha come effetto quello di provocare un certo indebolimento strutturale della superficie, e di portare alla comparsa di porosità e microfessurazioni le quali, ancorché invisibili se non al microscopio, pure forniscono punti di tenace attacco per sporcizia, residui, ecc.
Metodo di misura: EN ISO 10545 Parte 6 per le piastrelle non smaltate; EN ISO 10545 Parte 7 (Metodo PEI) per le piastrelle smaltate. Sono due metodi diversi, in quanto diverso è l’effetto dell’abrasione rispettivamente considerato. Nel caso delle piastrelle non smaltate, viene misurato il volume rimosso in particolari condizioni di abrasione (abrasione profonda). Una piastrella è considerata tanto più resistente, quanto minore è il volume di materiale rimosso. Per le piastrelle smaltate, viene realizzato un processo di abrasione superficiale di intensità crescente, e la valutazione degli effetti conseguenti viene condotta mediante un esame visivo in condizioni di osservazione specificate. In funzione dell’esito di tali osservazioni, alla piastrella misurata viene assegnata una classe di resistenza all’abrasione (Classe PEI 0, I, II, II, IV, V, in ordine crescente di resistenza). Va sottolineato che la classe di resistenza PEI V viene assegnata a piastrelle che, oltre a non evidenziare effetti visivi dopo abrasione, dimostrano di mantenere una adeguata resistenza alle macchie, e quindi una adeguata pulibilità.
Correlazioni con altre proprietà: La resistenza all'abrasione dipende dalla durezza e dalla compattezza dello strato superficiale. Il processo di abrasione è strettamente collegato al comportamento all'attacco chimico ed alle macchie.
Requisiti: Non vi è requisito minimo di accettabilità per la classe PEI: l'indicazione della classe deve servire al progettista per specificare correttamente la piastrella da usare per l'applicazione di interesse (un prodotto a bassa resistenza - Classe PEI I - può essere considerato idoneo per il pavimento di una camera da letto, ma non certamente per una pavimentazione esterna). Per quanto concerne il volume abraso - nel caso dunque delle piastrelle non smaltate - i requisiti di accettabilità sono via via meno severi - il volume abraso aumenta - all'aumentare dell'assorbimento d'acqua, come documentato in Tab. 3.II.
Discussione: Si rileva come gli andamenti osservati in Tab. 3.II inducano a specificare preferibilmente, per ambienti ad elevatissime sollecitazioni meccaniche superficiali, piastrelle non smaltare a struttura compatta: i Gruppi AI e AIIa, o i Gruppi BIa e BIb (non considerando i gruppi BII - piastrelle pressate non smaltaste con assorbimento d'acqua compreso fra il 3 e il 10 % - oggi non rappresentate sul mercato, almeno in Italia).
Resistenza all'attacco chimico e alle macchie
Definizione/descrizione: La resistenza all'attacco chimico è la caratteristica che definisce il comportamento della superficie ceramica a contatto con agenti chimicamente aggressivi, ossia potenzialmente in grado, per la loro composizione e caratteristiche chimiche, di reagire con la superficie ceramica stessa, corrodendola, penetrandovi in modo permanente o comunque alterandone l'aspetto estetico.
La resistenza alle macchie, strettamente collegata alla resistenza all’attacco chimico, definisce il comportamento della superficie ceramica a contatto con sostanze mac- chianti, ed è valutata in funzione dell’efficacia - e della facilità - con cui le macchie di definite sostanze, applicate sulla superficie stessa in condizioni specificate, possono venire rimosse. La resistenza alle macchie permette dunque di valutare la “pulibilità” di una superficie ceramica.
Metodo di misura: Resistenza all'attacco chimico: EN ISO 10545 Parte 13; Resistenza alle macchie: EN ISO 10545 Parte 14. Entrambe le prove si basano sulla valutazione in laboratorio degli effetti prodotti da sostanze chimiche (cloruro d'am- monio, ipoclorito di sodio, acido cloridrico, acido citrico, idrossido di potassio, ecc.), o sostanze macchianti specificate, mantenute a contatto, in accordo con procedure definite, con la superficie da provare per tempi predeterminati. Le sostanze macchianti sono state scelte in modo da rappresentare i tipici meccanismi di azione delle macchie: azione tracciante (da sostanze come gli inchiostri), azione chimica/ossidante (ad esempio, tintura di iodio), azione filmante (ad esempio, olio).
Il risultato è nella forma di una classe di resistenza all'attacco chimico da parte di ciascuno degli agenti chimici provati (Classe A = buona resistenza; Classe C = scarsa resistenza), e di una classe di resistenza a ciascun agente macchiante (Classe 5 = resistenza massima; Classe 1 = scarsa resistenza).
Correlazioni con altre proprietà: Le proprietà in esame sono influenzate sia dalla composizione chimica e mineralogica dello strato superficiale delle piastrelle, sia dalla sua struttura. La compattezza della superficie è certamente un fattore importante rispetto all'attacco chimico: quanto più compatta è la superficie, tanto minori sono le possibilità che le sostanze chimicamente aggressive e macchianti hanno di penetrarvi, per esercitare la rispettiva azione. Deve tuttavia essere considerata anche la distribuzione delle dimensioni dei pori sulla superficie, per cui materiali estrusi relativamente porosi hanno evidenziato comportamenti accettabili. Anche la rugosità è importante: una superficie liscia, oltre che compatta, è certamente meglio pulibile di una superficie rugosa.
I prodotti smaltati sono caratterizzati da una superficie vetrosa e compatta, e fra essi si possono trovare articoli con resistenza molto elevata all'attacco chimico ed alle macchie. Tuttavia, per le applicazioni in ambienti molto sollecitati, soprattutto per le pavimentazioni, non bisogna trascurare la prevedibile variazione di resistenza chimica con l'uso, determinata dall'abrasione (dalla progressiva rimozione dello strato più superficiale di smalto, con conseguente “apertura” di microporosità). La previsione di questo effetto è possibile, come osservato nella precedente sezione dedicata alla resistenza all’abrasione, mediante il metodo EN ISO 10545 Parte 7, che consiglia la misura della resistenza alle macchie dopo abrasione.
Requisiti: Le specifiche di prodotto contenute negli allegati a EN 14411 riportano dei limiti di accettabilità, per tutti i tipi di piastrelle (dei gruppi A e B), limitatamente alla resistenza ai prodotti chimici di uso domestico (Classe B o superiore) ed alla resistenza alle macchie delle piastrelle smaltate (Classe 3 o superiore).
Discussione: E' evidente che il solo rispetto di questi requisiti non basta per le applicazioni in ambienti con forti sollecitazioni di tipo chimico a carico della superficie: il progettista dovrà concentrare la propria scelta su prodotti dotati dei livelli massimi di resistenza.
Cessione di piombo e cadmio
Definizione/descrizione: La cessione di piombo e cadmio è una caratteristica chimica - oltre che di sicurezza - applicabile alle piastrelle smaltate. Il controllo di questa caratteristica è consigliabile soprattutto per le piastrelle da applicare su superfici destinate a venire a contatto con sostanze alimentari, le quali sono almeno potenzialmente in grado di estrarre, contaminandosi, appunto piombo e cadmio - due metalli talora contenuti negli smalti - dalla superficie smaltata.
Metodo di misura: EN ISO 10545.15. La superficie smaltata viene mantenuta a contatto, per un tempo ed in condizioni specificate, con una soluzione di acido acetico. Successivamente si misura il quantitativo di piombo e cadmio rilasciati in soluzione. I valori vengono riferiti all’unità di superficie esposta, e dunque espressi in mg/dm2.
Correlazioni con altre proprietà: è una caratteristica chimica correlata, come per altro la resistenza all’attacco chimico, alla composizione ed alla struttura dello smalto. In generale il rischio di cessione è tanto maggiore quanto maggiore è il contenuto degli elementi in esame e quanto più bassa è la temperatura di cottura. Le piastrelle di ceramica italiane reperibili sul mercato possono essere considerate sicure sotto questo profilo.
Requisiti: La norma EN 14411 non prescrive nessun requisito in merito, per nes- suno dei gruppi di prodotti. Indica invece la disponibilità del metodo di misura sopra citato, che potrà essere utilizzato sulla base di uno specifico accordo fra venditore ed acquirente.
Resistenza allo scivolamento
Definizione/descrizione: La scivolosità di una superficie è la caratteristica che descrive le condizioni cinematiche e dinamiche di movimento di un corpo a contatto con essa. Un parametro utilizzato per caratterizzare la scivolosità di una superficie è il coefficiente di attrito, statico o dinamico, al quale è proporzionale la forza, parallela alla superficie di contatto, che occorre applicare perché si abbia moto relativo fra due corpi, e quindi anche la forza che ne definisce le condizioni di equilibrio. Quanto più alto è il coefficiente di attrito, tanto minore è la scivolosità.
Il coefficiente di attrito dipende dalla natura dei due corpi a contatto, e dalle condizioni del contatto stesso: in particolare, dallo stato delle superfici, dalla presenza di eventuali materiali interposti, dalle condizioni di umidità e temperatura, ecc.
Per quanto concerne la natura delle superfici, per i materiali da pavimento (a contatto con la suola di una calzatura) il coefficiente di attrito è tanto più basso quanto più la superficie è liscia, lucida, indeformabile, cioè resistente al punzonamento, quanto maggiore è la tendenza che essa ha a lasciarsi ricoprire da un film sottile e continuo d'acqua, ecc.; rispetto a quello della superficie asciutta e pulita, il coefficiente di attrito diminuisce in presenza di oli, grassi, sporcizia, acqua, tutti materiali che, comportandosi allo stesso modo di lubrificanti fra la suola e la superficie del pavimento, aumentano la scivolosità e quindi i rischi di cadute ed infortuni.
Le superfici caratterizzate invece da un valore più elevato del coefficiente di attrito sono quelle scabre, rugose; tale rugosità può essere, per così dire, naturale, oppure può essere volutamente creata, per mezzo della realizzazione di rilievi opportunamente sagomati e dimensionati. Tali superfici mantengono valori relativamente elevati del coefficiente di attrito anche in presenza di acqua o di altri liquidi, dal momento che i rilievi citati inibiscono la formazione di un film continuo, responsabile appunto della diminuzione di attrito.
Metodo di misura: La discussione sui metodi di misura è ancora in corso presso i relativi comitati tecnici CEN e ISO. Sono disponibili e praticati quattro diversi metodi, i cui risultati sono difficilmente correlabili l'uno all'altro.
Metodo A: coefficiente di attrito dinamico, misurato con dispositivo automatico portatile (BCR Tortus);
Metodo B: coefficiente di attrito statico. misura basata sul metodo ASTMC1028;
Metodo C: scivolamento su piano inclinato, metodo derivato da DIN 51130;
Metodo D: metodo del pendolo.
Correlazioni con altre proprietà: La resistenza allo scivolamento di un materiale da pavimentazione dipende essenzialmente dalla rugosità della sua superficie, e dalla presenza di rilievi superficiali in grado di assicurare il drenaggio di eventuali
liquidi, e quindi buone condizioni di aderenza fra suola e superficie anche in condizione di pavimentazione bagnata. Pure in questo caso dobbiamo sottolineare che la scelta di un materiale da pavimentazione dotato di idoneo coefficiente di attrito è condizione solo necessaria per ridurre o prevenire i rischi di scivolamento: l'assicurazione, mediante la predisposizione di adeguate pendenze, di condizioni di efficace deflusso delle acque (meteoriche o di lavaggio o processo, a seconda dei casi) è non meno determinante.
Le caratteristiche fisiche della superficie associate ad una buona resistenza allo scivolamento (elevata rugosità, rilievi, ecc.) sono opposte a quelle che sottendono ad una efficace ed efficiente pulibilità (bassa rugosità, assenza di rilievi o anfratti in grado di ospitare e trattenere tenacemente lo sporco). E’ un contrasto risolubile solo ricorrendo a prodotti a superficie rugosa e con rilievi, ma dotati di eccellenti livelli di resistenza all’abrasione ed all’attacco chimico, e quindi in grado di sopportare senza deteriorarsi azioni di pulizia particolarmente vigorose dal punto di vista meccanico e chimico. Le piastrelle di ceramica includono molti prodotti conformi a questa specifica.
Requisiti: E' rilevante il requisito stabilito, in Italia, dalla Legge n° 13/89 e dal successivo Decreto Ministeriale 14/06/89, n° 236, relativi alle prescrizioni tecniche ai fini del superamento e dell'eliminazione delle barriere architettoniche. In questa legge viene fissato, per i pavimenti di ambienti pubblici, un valore minimo ammissibile del coefficiente di attrito dinamico, misurato con il Metodo A (BCR Tortus) sopra citato, pari a 0,40.
Articolo tratto da "Le piastrelle di ceramica negli ambienti pubblici - Manuale applicativo", edito ad Edi.Cer. S.p.A., a cui si rimanda per proseguire la lettura e gli approfondimenti.
Clicca sull'immagine per andare al Manuale.
Architettura
L'architettura moderna combina design innovativo e sostenibilità, mirando a edifici ecocompatibili e spazi funzionali. Con l'adozione di tecnologie avanzate e materiali sostenibili, gli architetti moderni creano soluzioni che affrontano l'urbanizzazione e il cambiamento climatico. L'enfasi è su edifici intelligenti e resilienza urbana, garantendo che ogni struttura contribuisca positivamente all'ambiente e alla società, riflettendo la cultura e migliorando la qualità della vita urbana.
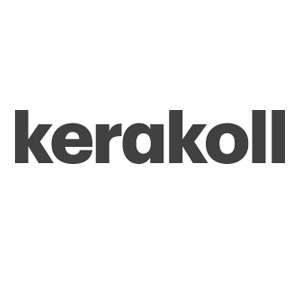
Ceramica
Ceramica: tutto su pavimenti e rivestimenti, adesivi, posa, patologie, manutenzione e design. Articoli tecnici e di tendenza per progettisti, imprese, applicatori e professionisti delle finiture.

Pavimenti per Interni
Tutto quello che devi sapere sulle pavimentazioni per interni: le tipologie di rivestimento più comuni, le soluzioni tecniche più innovative, gli...