Ingegneria digitale a valore aggiunto dietro le quinte del Palazzo Europa di Bruxelles
Ingegneria digitale che ottimizza, rendendo più snella e rapida, la progettazione e la produzione edile. Un unico ambiente informativo permette ai progettisti di simulare, sperimentare e validare ogni minimo componente, perfezionando e accelerando le attività in cantiere.
Palazzo Europa: la modellazione parametrica ne ha accelerato notevolmente la realizzazione
Ingegneria digitale significa avvalersi della migliore innovazione per abilitare una modellazione 3D che permette di creare un modello digitale basato su una serie di parametri elaborati da algoritmi preprogrammati. La modellazione parametrica è la chiave che ha permesso di finalizzare in pochi mesi la realizzazione della pelle della lanterna del Palazzo Europa, sede principale del Consiglio europeo e del Consiglio dell'Unione Europea a Bruxelles. Nato come intervento di ristrutturazione e ampliamento di un precedente edificio storico, il progetto è firmato Philippe Samyn and Partners, Studio Valle e Buro Happold.
La sua peculiarità è l’impostazione dell’opera in cui un volume esterno cubico ne contiene uno interno, chiamato lanterna. Quest’ultima, infatti, è una struttura caratterizzata da un volume multilivello a sezione ellittica variabile che ospita sale per riunioni e conferenze nonché sale per la stampa.
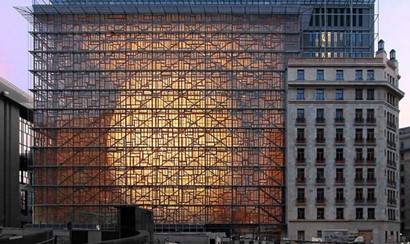
Ingegneria digitale: i vantaggi dell’innovazione 3D
Più in dettaglio, il volume della lanterna è generato dalla rotazione di ellissi sovrapposte: allargandosi al centro, colloca nei livelli più bassi e più alti gli spazi di dimensioni minori e la sala da 250 posti, la più grande nella parte centrale più larga. Di notte la struttura è illuminata da 374 tubi a Led che, integrati all'interno dell’involucro esterno, proiettano la loro luce sulla trama obliqua disegnata sui pannelli vetrati curvi che lo avvolgono, materializzando una grande e suggestiva lanterna luminosa lungo Rue de la Loi.
A occuparsi di risolvere la complessità realizzativa della pelle della lanterna è stato lo studio italiano VLP+P che ha ottimizzato l’intero processo di studio e definizione dei requisiti configurativi, avvalendosi dell’ingegneria digitale per finalizzare al meglio le modalità costruttive. Utilizzando 3DEXPERIENCE Platform di Dassault Systèmes, i progettisti hanno creato un gemello digitale dell’opera che ha consentito di studiare in un ambiente virtuale geometrie, angoli di curvatura e tolleranze, supportati da una capacità elaborativa potenziata che ha perfezionato i risultati e accelerato i tempi e i modi dello sviluppo e della produzione.
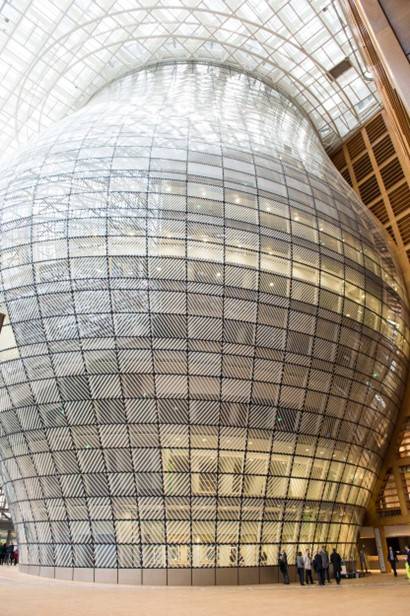
3 sfide progettuali risolte grazie all’ingegneria digitale
Entrando più nel merito del progetto, la lanterna del Palazzo Europa è una struttura che si sviluppa su 12 piani, rivestita in vetro a doppia curvatura. A questo proposito:
- La prima grossa sfida affrontata da VLP+Partner è stata risolvere la fattibilità dell’idea architettonica rispetto alle tecniche produttive disponibili;
- La seconda sfida è stata risolvere la progettazione di tutti i sistemi di staffaggio in acciaio, caratterizzati da diverse configurazioni geometriche;
- La terza sfida importante è stata quella di progettare nel modo migliore la compartimentazione al fuoco.
Come risolvere la doppia curvatura delle lastre in vetro
La tecnologia consentiva di fare curvature del vetro con raggi differenti su ciascun pezzo, il che avrebbe allungato a dismisura le tempistiche di realizzazione. Avvalendosi dell’ingegneria digitale, tutte le lastre vetrate sono state ottimizzate per essere producibili in singola curvatura. VLP+P ha utilizzato la modellazione parametrica per generare un gemello virtuale (digital twin) della lanterna, partendo poi con lo studio della superficie di una prima lastra con una curvatura variabile da 15 m a 17 m.
Ottimizzando il vetro a doppia curvatura, sostituito con elementi cilindrici, molto più facili e meno costosi da produrre, gli esperti hanno individuato l’asse del cilindro che approssimava al meglio la superficie reale della lastra. Questo cilindro, una volta ritagliato sulla sagoma della superficie originaria, ha permesso di effettuare le opportune verifiche tra la superficie iniziale e quella ottimizzata, confermando tolleranze e differenze talmente minime da garantirne la riproducibilità in cantiere. Nell’ambiente digitale, l’operazione di calcolo eseguita su una singola lastra è stata poi ripetuta automaticamente dal sistema per 1700 volte, ovvero per tutte le lastre di vetro necessarie a rivestire l’intera struttura. Discretizzando le geometrie con le superfici cilindriche e mantenendo inalterate le caratteristiche estetiche del progetto finale, VLP+P ha potuto condividere con il produttore del vetro i costruttivi di tutte le lastre con i relativi raggi di curvatura, il che ha velocizzato il lavoro degli operai in fabbrica e in cantiere.
L'ARTICOLO CONTINUA NEL PDF IN ALLEGATO...
Condividi su: Facebook LinkedIn Twitter WhatsApp