I criteri di scelta per un sistema resinoso per pavimentazione industriale
Un articolo di inquadramento generale per chi vuole capire meglio e più a fondo i criteri di valutazione utili alla scelta della “soluzione minima” più corretta quando si sta valutando un sistema resinoso per il trattamento di una pavimentazione industriale.
UNI 10966: il riferimento normativo per una corretta scelta del sistema resinoso
Un po’ invidio quelle aziende mono prodotto che hanno fatto della semplicità di scelta della soluzione da proporre il loro punto di forza delle strategie di vendita e, a volte, del loro successo commerciale. Dico “un po’ invidio”, perché se da un lato la scelta diventa più semplice, per non dire scontata, dall’altro si perde il gusto e il bello della capacità di valutazione del problema da risolvere applicando le proprie conoscenze e abilità professionali. Queste ultime non sono un segreto o una chimera irraggiungibile; personalmente, ad esempio, se non posso acquisirle in un determinato campo cerco di sfruttare quelle altrui e gli aiuti che mi vengono dati.
Questo pomposo avvio di articolo vuole essere uno spunto per il lettore che vuole capire meglio e più a fondo i criteri di valutazione utili alla scelta della soluzione minima più corretta quando si sta valutando un sistema resinoso per il trattamento di una pavimentazione industriale.
Ho volutamente scritto “scelta…minima”, perché questa stabilisce un limite sotto il quale non si dovrebbe andare. Optare, invece, per qualcosa di più performante non è mai un errore; nella peggiore delle ipotesi può diventare un esercizio di inutilità.
Se io fossi un progettista, cosa mi sarebbe d’aiuto per orientarmi nella scelta del sistema resinoso più corretto per soddisfare le esigenze tecniche ed economiche del mio committente? O, sul fronte opposto, se io, responsabile della manutenzione industriale, avessi il compito di stabilire se la soluzione che mi stanno offrendo è idonea a soddisfare i miei bisogni, quali strumenti di valutazione avrei a disposizione?
Un grande aiuto per entrambe le figure, e per tutte quelle che in modo simile si trovano a dover affrontare lo stesso problema, arriva dalla norma UNI 10966 che al capitolo 7.3 offre un’utile tabella di valutazione per orientare alla scelta di un sistema resinoso per una pavimentazione industriale. Con questo articolo proverò ad ampliare quelle informazioni, fornendo maggiori dettagli e precisazioni e dando qualche esempio che, nella vastità delle casistiche possibili, non potrà essere mai totalmente esaustivo. Ogni pavimentazione ha vita e caratteristiche proprie, pertanto le informazioni che seguiranno, per quanto basate su fondamenti tecnici e lunga esperienza, non potranno tenere conto delle immancabili eccezioni che rendono così vere le regole.
Prima di addentrarci tra stratigrafie di materiali diversi, spessori da applicare, formule chimiche di prodotti resinosi, forme di attrezzi e attrezzature varie, facciamo un elenco di cosa ci serve sapere per una corretta progettazione del sistema resinoso.
Quali sono quindi i fattori e le informazioni di cui abbiamo bisogno? In breve, li riassumo come segue:
- tipo e condizioni del supporto da trattare;
- destinazione d’uso della pavimentazione e, quindi, sollecitazioni cui verrà sottoposta;
- esigenze e aspettative dell’utilizzatore finale.
Qualcuno ci aggiungerebbe anche il budget a disposizione dell’utente finale. Ovvio che tale fattore è importantissimo, non però ai fini di “cosa” fare, ma eventualmente di “quanto farne”. Il mio consiglio, e non solo il mio, è di non scendere mai a compromessi tecnici per venire incontro al budget, ma piuttosto di valutare, dove possibile, di trattare una superficie più ridotta di quella pensata inizialmente. Facciamone meno, ma facciamolo bene.
Per la definizione e la descrizione dei sistemi che verranno di seguito citati si fa esplicito rimando al capitolo 7.1 della UNI 10966.
Tipo e condizioni del supporto
Nell’ambito delle pavimentazioni industriali è indubbio che il supporto più comune sia il calcestruzzo che costituisce, a occhio, il 90% delle casistiche. Meno frequenti i supporti costituiti da piastrelle, mentre altre tipologie quali i massetti cementizi, l’acciaio, il legno, i rivestimenti resilienti e altri ancora sono un evento abbastanza raro.
Il calcestruzzo è (non è – potrebbe essere – magari lo fosse…scegliete voi) un materiale eccezionale, ma ha i suoi limiti intrinsechi, almeno nel mondo delle pavimentazioni industriali. È dualisticamente una bella e una brutta “bestia”. Per fare degli esempi banali e già noti a tutti, possiede ottime resistenze meccaniche ed è duraturo, ma patisce le aggressioni chimiche da parte delle sostanze acide e non è perfettamente impermeabile ai liquidi in genere.
I suoi “limiti” possono aver lasciato il segno su pavimentazioni già in uso; non è infatti raro trovarsi di fronte a supporti inquinati, impregnati di oli, con scalfitture, crepe e irregolarità superficiali, polverosi eccetera.
I sistemi resinosi a basso spessore, quali le impregnazioni e i sistemi a film sottile colorati, sono perfetti su supporti lisci e puliti e se sufficienti a soddisfare le prestazioni richieste dall’uso, ma su supporti inquinati si renderanno necessarie operazioni di pulizia, bonifica e riparazione superficiale che richiederanno spessori di resina più consistenti per coprire le inevitabili irregolarità superficiali. Se tali operazioni di pulizia consistono in una levigatura a diamante, un sistema resinoso a film ad alto spessore è già sufficiente a realizzare un grado di finitura abbastanza regolare. Su superfici per le quali viene invece richiesto un trattamento più incisivo quale la pallinatura o una scarifica, si dovrà valutare come minimo un sistema multistrato di spessore adeguato. Una regola empirica, col metodo scientifico universalmente riconosciuto come “spannometro”, suggerisce che la rugosità superficiale del supporto dopo il trattamento meccanico di preparazione non sia maggiore di un terzo dello spessore del sistema da applicare. Prendete questo suggerimento con i dovuti benefici d’inventario.
Per i supporti in piastrelle vale lo stesso discorso. Premesso che tali supporti vanno levigati a diamante e/o pallinati prima della posa della resina, alla rugosità superficiale conseguente al trattamento di preparazione si aggiungono le irregolarità delle fughe tra le piastrelle. Se chiediamo al sistema resinoso di non marcare visivamente la presenza delle fughe sottostanti, per motivi puramente estetici, necessiteremo di almeno un paio di strati di rasatura preliminare. Tali supporti richiedono quindi almeno un sistema multistrato o autolivellante di alcuni millimetri di spessore, o meglio ancora un massetto di malta resinosa o di poliuretano-cemento. I massetti di malta resinosa richiedono quasi sempre uno strato di finitura costituito da un sistema autolivellante o multistrato, che ne caratterizza le proprietà finali.
Una nota doverosa sui sistemi autolivellanti con finitura lucida e molto riflettente: su supporti in piastrelle o che sono stati scarificati, e in generale su tutti i supporti esistenti la cui superficie presenta qualche irregolarità, non pretendiate di ottenere sempre un aspetto finale del sistema resinoso come se fosse una pietra tombale perfettamente levigata e planare. Una finitura opaca, anziché lucida come uno specchio, ha il pregio di nascondere le naturali ondulazioni e minime irregolarità della superficie, ma potrebbe avere, e sottolineo il condizionale, maggiore tendenza a trattenere lo sporco.
Ho fin qui tralasciato ogni considerazione in merito all’umidità del supporto. La presenza di acqua, sia essa residua della maturazione del calcestruzzo, derivante dai processi di lavorazione o di lavaggio o di risalita capillare, è il fattore principale nella scelta del tipo di prodotto resinoso da utilizzare, che deve essere traspirante o comunque idoneo per i fondi umidi, così come lo sono i prodotti epossi-cemento o poliuretano-cemento. In alcuni casi si possono però realizzare anche sistemi con prodotti non traspiranti, ad esempio per un massetto di malta resinosa di almeno 8-10 mm di spessore, sul quale verrà successivamente applicato un sistema multistrato o autolivellante.
Destinazione e sollecitazioni d’uso
La valutazione dello spessore minimo da applicare in funzione delle condizioni del supporto è solo il primo passo, che si spera sia verso la gloria.
L’avrete sicuramente sentito dire fino alla noia, a volte con toni reboanti ed enfatici: “la pavimentazione è, per sua natura, l’elemento più sollecitato di un edificio!”. Verissimo, ma talvolta dimenticato o sottovalutato.
Rimanendo nell’ambito industriale, e mettiamoci anche del terziario, chi progetta un sistema resinoso per una pavimentazione deve sapere cosa ci accadrà sopra. Scontato? Sì, o forse no, talvolta forse. Se devo progettare un sistema resinoso per una milonga, vado sul sicuro con un sistema autolivellante verde, così faccio felice anche Paolo Conte. Ma le cose si complicano quando l’utilizzo è più industriale, con le innumerevoli variabili che possono caratterizzarlo. La pura informazione della destinazione d’uso dei locali non è sempre di per sé elemento sufficiente. Sapere che ci sarà un magazzino, una lavorazione carni o un confezionamento di farmaci è un’informazione importantissima, ma sarebbe bene sapere qualcosa di più in merito al tipo di carichi statici o dinamici, tipo e frequenza dei lavaggi, eventuale presenza di polveri o detriti che aumentano l’effetto abrasivo, presenza di liquidi e loro temperatura, natura e concentrazione degli aggressivi chimici e via discorrendo.
A maggiori sollecitazioni, in termini di intensità e/o durata nel tempo, deve corrispondere anche, ma non solo, un maggiore spessore del sistema resinoso.
La tabella al capitolo 7.3 della UNI 10966 elenca le sollecitazioni e le caratteristiche richieste più frequenti per una pavimentazione ad uso industriale e suggerisce quali sistemi resinosi possono essere idonei per tale scopo. Vediamone qualcuno più in dettaglio.
Transito di mezzi e personale – sollecitazioni meccaniche
Per ambienti caratterizzati da un traffico modestissimo di mezzi e persone un sistema impregnante o a film a basso spessore è sufficiente per mantenere la pavimentazione facile da pulire e, magari, anche esteticamente piacevole. Il ridotto spessore di queste soluzioni non è più sufficiente già in presenza di qualche transpallet o di sversamenti accidentali di liquidi.
I transpallet sembrano piccoli e leggeri, ma la loro azione è in realtà molto aggressiva. Possono portare 10-12 quintali muovendosi su ruote piccole e dure, manovrando spessissimo come dei contorsionisti in spazi ristretti che comportano forti sollecitazioni di torsione da parte delle ruote sulla superficie del pavimento. Uno sistema resinoso troppo avaro di spessore mostrerà in beve tempo zone di usura fino a esporre il supporto (ah, non ve l’avevo detto? Il sistema resinoso indistruttibile non esiste…). Un film ad alto spessore, che suggerirei non minore di mezzo millimetro, realizza già una buona protezione, ma prima o poi (e normalmente più prima che poi) necessiterà dell’applicazione di almeno una mano di prodotto resinoso di manutenzione.
Per aree di stoccaggio e di produzione soggette a un traffico veicolare e di personale intenso, anche in presenza di caduta di oggetti, si deve optare almeno per un sistema autolivellante o multistrato, di spessore crescente in funzione dell’intensità delle sollecitazioni; per condizioni particolarmente severe si prendano anche in considerazioni sistemi di almeno 5 mm.
Presenza di liquidi e aggressioni chimiche
La presenza frequente o costante di liquidi, anche la semplice acqua, è una sollecitazione sempre severa per la pavimentazione.
Il sistema resinoso deve risultare sufficientemente spesso da non subire danni o perforazioni quando sottoposto all’uso quotidiano, in conseguenza di urti o trascinamenti di oggetti. Una scalfittura che interessasse tutto lo spessore del sistema permetterebbe ai liquidi di penetrare nel supporto. Il buchino diventerebbe un buco, poi un buco più largo ancora e ben presto il danno si distribuirebbe nella zona circostante.
La norma UNI 10966 suggerisce minimo 2 mm di sistema resinoso quando si ha presenza di liquidi, ma qui vi inviterei caldamente a considerare almeno 3 mm.
Il sistema multistrato, con una finitura sufficientemente ruvida per garantire un minimo di sicurezza sulla superficie bagnata e una buona resistenza chimica generale, si adegua perfettamente a questa situazione, ma nel caso in cui i liquidi siano chimicamente molto aggressivi e/o molto caldi, o analogamente si effettuino frequenti pulizie e sanificazioni con getti di vapore, i sistemi resinosi ad alte prestazioni a base di prodotti poliuretano cemento di almeno 4 mm di spessore sono l’unica soluzione percorribile.
La resistenza agli shock termici e alle temperature di esercizio di questi sistemi dipende dal loro spessore, che può arrivare fino a una dozzina di millimetri, ma sono comunque ben superiori a qualsiasi altra tipologia di prodotto. Si possono applicare in celle frigorifere che lavoreranno a -40°C e possono sopportare sbalzi termici o temperature di esercizio fino a +120°/+130°C! Situazioni del genere sono tipiche e frequenti nelle aziende alimentari, dove i prodotti poliuretano-cemento trovano largo uso.
Questi sistemi richiedono minima manutenzione (ho detto minima, non assente…) e lunga aspettativa di vita utile di esercizio. Esistono tuttora pavimenti rivestiti con tali prodotti, magari di aspetto non proprio decorativo ma perfettamente funzionanti, realizzati quando andavo ancora alle scuole elementari, quindi…vabbè, millanta anni fa.
Igienicità, facilità di sanificazione
Una superficie ruvida e antiscivolo è condizione sine qua non quando la sicurezza dei lavoratori e dei mezzi che transitano sulla pavimentazione bagnata è caratteristica fondamentale e, aggiungo, doverosa.
Ma ruvido non va sempre d’accordo con facile da pulire; quindi la scelta del tipo di profilo superficiale da conferire al sistema resinoso va attentamente valutata. In alcune situazioni l’esigenza di facilità di pulizia e sanificazione è tale da richiedere una superficie perfettamente liscia ed ermetica.
A solo titolo di esempio, citiamo le sale operatorie e gli ambienti sterili e sanitari in genere, i locali di confezionamento di farmaci, l’industria ottica ed elettronica e tutti gli ambienti lavorativi soggetti a regime di camere bianche.
Per tali aree si utilizzano sistemi autolivellanti lisci, per lo più a base di resine epossidiche, di almeno 2 mm di spessore, prescrivendo spesso sistemi resinosi a film anche per le pareti a tutta altezza e i soffitti. Per chi volesse approfondire il tema delle soluzioni per le camere bianche faccio esplicito rimando a un mio precedente articolo in merito, pubblicato su questo portale.
Planarità
I limiti di tolleranza di planarità indicati dalla UNI 10966 nel prospetto nr. 3 al capitolo 5.1.5.2., presi a prestito dalle disposizioni tecniche per i massetti in calcestruzzo, possono risultare troppo ampi per situazioni particolari, ad esempio in presenza di carrelli elevatori che lavorano in corsie di scaffali molto elevati o quando si installano impianti produttivi particolari.
La planarità deve essere possibilmente già rispettata nel supporto, perché i relativamente limitati spessori dei sistemi resinosi non la possono modificare in maniera apprezzabile. Fanno eccezione i massetti di malta resinosa, che non possono fare miracoli ma sono capaci, entro certi limiti e con opportune tecniche di posa, di correggere la planarità del supporto esistente per farla contenere in limiti di tolleranza più ristretti.
Impermeabile e impermeabilizzazione
L’impermeabilità ai liquidi dei sistemi resinosi, garantita a partire dai film ad alto spessore, è una caratteristica comune che dipende dallo spessore e dalla natura dei materiali impiegati. Sistema impermeabile e sistema impermeabilizzante non sono la stessa cosa, in quanto la seconda proprietà dipende anche dalla capacità del sistema di non avere interruzioni dello strato, che consentirebbero il passaggio del liquido.
Nel caso dei sistemi resinosi per le pavimentazioni, che sono e devono essere completamente aderenti al loro supporto, chi la fa da padrone nei movimenti di assestamento e di dilatazione termica è il massetto in calcestruzzo avente spessore di diversi centimetri, non certo i pochi millimetri di strato resinoso. È il primo che “trascina” il secondo, non il contrario; non sarà la migliore delle descrizioni accademiche, ma sono certo che rende bene l’idea. Ne consegue che se il massetto in calcestruzzo di supporto si fessura per qualsiasi motivo, anche il sistema resinoso soprastante si fessurerà a sua volta, esattamente nello stesso punto. Vale anche quando il sistema resinoso viene applicato a sormonto dei giunti di controllo, che dovrebbero essere statici e spesso statici non sono, o di crepe già esistenti stuccate durante le fasi preliminari di posa del sistema. Non sono fortunatamente situazioni frequenti, e quando capitano sono facilmente riparabili, anche se esteticamente visibili.
Vi sono tuttavia situazioni in cui viene richiesta la più ampia continuità degli strati di resina anche per ampie superfici, per evitare infiltrazioni di liquidi che potrebbero inquinare la falda o percolare ai piani sottostanti.
Il caso più frequente è comunque quello delle pavimentazioni dei parcheggi nelle aree geografiche dove vengono utilizzati sali disgelanti, che sono a base di cloruro di calcio. I cloruri sono solubili in acqua e se grazie ad essa penetrassero nel supporto in calcestruzzo potrebbero essere veicolati fino ai ferri di armatura in acciaio innescando pericolosi processi di corrosione. Fatevi un giro in rete con un buon motore di ricerca, e troverete più di una situazione in cui il processo di corrosione ha portato al totale degrado delle armature con conseguente collasso della soletta. Il problema è ovviamente particolarmente sentito per le aree di parcheggi in esterni, esposte alle intemperie e allo spargimento dei sali, ma si può presentare anche nelle aree al coperto a causa dell’acqua che può essere veicolata dagli pneumatici.
Per tali pavimentazioni esistono sistemi resinosi multistrato realizzati principalmente con resine poliuretaniche o poliureiche caratterizzati da un’elevata elasticità, che permette loro di far ponte, entro certi limiti, sui movimenti di fessure o giunti già esistenti sul supporto o sulla formazione di nuove lesioni, mantenendo così inalterata la caratteristica impermeabilizzante. Tale proprietà è conosciuta col termine anglofono di crack-bridging e si distingue in diverse classi di ampiezza di escursione cui il sistema è in grado di far ponte. Vien da sé che i sistemi multistrato per superfici esterne, più sollecitate dinamicamente perché direttamente esposte all’insolazione estiva e al gelo invernale, avranno una stratigrafia più complessa di quelli che si utilizzano per le superfici interne.
Un importante e fondamentale precisazione: i sistemi resinosi elastici dotati di elevata proprietà crack-bridging sono stati studiati per proteggere il supporto in calcestruzzo su cui vengono applicati e non devono essere considerati, mai e poi mai, sostituitivi della tradizionale impermeabilizzazione realizzata con manti sintetici o bituminosi o che dir si voglia.
’o Sole mio… Rivestimenti resinosi per l'outdoor
Per rimanere in ambito di soluzioni per pavimentazioni esterne, per fortuna piuttosto rare, va precisato che non tutti i prodotti resinosi sono compatibili con tale uso.
I sistemi a base di resina epossidica sono di solito utilizzati limitatamente alla protezione chimica di strutture in calcestruzzo quali vasche di contenimento, plinti e pilastri di serbatoi di sostanze chimiche, depuratori eccetera. Le resine epossidiche hanno la tendenza a ingiallire e talvolta a sfarinare leggermente quando esposte direttamente alla luce solare. In realtà, se applicate a pavimento, il problema sarebbe prevalentemente estetico. Per ovviare all’inevitabile ingiallimento è uso comune applicare una mano di finitura a base di resine poliuretaniche alifatiche, caratterizzate da un’ottima stabilità ai raggi UV e alle intemperie in genere.
Eviterei sistemi con finitura liscia, a meno che non siate dei fan dell’Holiday on Ice.
Anche i sistemi ad alte prestazioni a base di poliuretano-cemento sono un’ottima e valida soluzione per esterni. Non risentono minimamente delle condizioni di esposizione alle intemperie, fatto salvo un rapidissimo e vistoso ingiallimento e viraggio di colore della loro superficie. Sono spesso utilizzati in baie di carico e scarico di prodotti corrosivi, soggette non solo al contatto delle sostanze chimiche, ma anche al transito di autobotti e frequenti urti delle flange terminali di tubazioni flessibili.
[...] Continua la lettura nel PDF allegato
L'articolo prosegue con la descrizione dei principali fattori che influenzano i criteri scelta del sistema resinoso quando si tratta di assecondare esigenze e aspettative dell’utilizzatore finale.
Normativa Tecnica
Con questo TOPIC raccogliamo le news e gli approfondimenti che riguardano il tema della normativa tecnica: le nuove disposizioni, le sentenze, i pareri e commenti, l’analisi di casi concreti, il commento degli esperti.
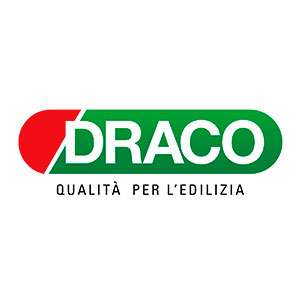
Pavimenti Industriali
Con il topic "pavimento industriale" vengono raccolti tutti gli articoli pubblicati sul Ingenio su queste tipologie di pavimentazioni in calcestruzzo e riguardanti la normativa, la progettazione, l'applicazione, l'innovazione tecnica, i casi studio, i controlli e i pareri degli esperti.
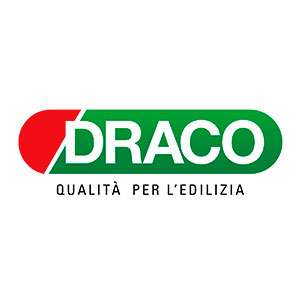
Pavimenti per Esterni
Le pavimentazioni outdoor, che spaziano dalle superfici per terrazze ai camminamenti nei giardini, dai bordi piscina fino alle pavimentazioni...

Pavimenti per Interni
Tutto quello che devi sapere sulle pavimentazioni per interni: le tipologie di rivestimento più comuni, le soluzioni tecniche più innovative, gli...

Progettazione
La progettazione costituisce un passaggio fondamentale nell’intero processo edilizio, poiché determina in maniera significativa la qualità, la...
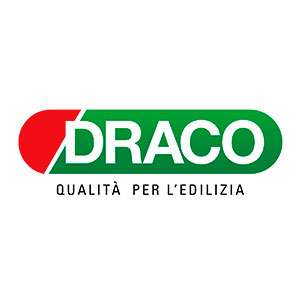
Resina
I sistemi resinosi continui rappresentano una versatile gamma di soluzioni per la protezione e il miglioramento delle caratteristiche delle...
Condividi su: Facebook LinkedIn Twitter WhatsApp