4 requisiti dei pavimenti in grès nell’industria alimentare, nelle attività di ristorazione e del commercio
Quali caratteristiche devono avere le pavimentazioni in grès porcellanato tecnico se vengono installate in ambienti destinati alla produzione e lavorazione degli alimenti? Ecco qui un articolo di approfondimento.
Classificazione delle attività economiche che si occupano di produzione e trasformazione degli alimenti
Quando si parla di industria alimentare si fa riferimento a un’ampia e varia gamma di imprese coinvolte nel trattamento degli alimenti. La materia prima, proveniente dall’agricoltura e dall’allevamento o pesca, viene dall’industria alimentare trasformata in prodotti di consumo più o meno immediato o conservabile.
In relazione al grado di trasformazione raggiunto, le industrie alimentari si distinguono in:
- Industrie di prima trasformazione, che trasformano la materia prima in un semilavorato;
- Industrie di seconda trasformazione, che trasformano i semilavorati in prodotti finiti destinati al consumo.
Mentre dal punto di vista tecnologico, le industrie alimentari si distinguono in:
- Estrattive (produzione es. zucchero da bietole);
- Fermentative (produzione es. vino e della birra);
- Conserviere (es. industrie dolciarie, torrefazioni etc.).
Secondo la classificazione delle attività economiche ATECO (2007) fanno parte della divisione 10 - Industria Alimentare le aziende che si occupano della “trasformazione di prodotti dell'agricoltura, della silvicoltura e della pesca in alimenti e bevande commestibili per l'uomo o per gli animali, nonché la produzione di vari prodotti intermedi da non considerare alla stregua dei prodotti alimentari (ad esempio, pellame proveniente dai macelli, panelli provenienti dalla produzione di olio)”.
La divisione 10 ATECO è organizzata per attività riguardanti diversi tipi di prodotti: carne, pesce, frutta e ortaggi, grassi ed oli, prodotti lattiero-caseari, granaglie, prodotti di panetteria e farinacei, altri prodotti alimentari e mangimi per animali. Questa divisione non include la preparazione di pasti per il consumo immediato come nel caso di ristoranti, quest’ultima classificata nella divisione 56 - Attività di ristorazione.
Nel caso in cui la lavorazione sia minima e non conduca ad una reale trasformazione, l'attività viene classificata nella divisione Commercio all'ingrosso e al dettaglio (sezione G - 47.2).
Photo courtesy Cipa Gres
Vantaggi e requisiti dei pavimenti ceramici in grès tecnico nel settore alimentare
I vantaggi offerti dall’uso del grès porcellanato tecnico per la realizzazione di pavimentazioni nel settore alimentare sono molteplici:
- Resistenza al gelo;
- Resistenza agli sbalzi termici;
- Resistenza al sale;
- Resistenza agli acidi;
- Resistenza a muffe e trattamenti;
- Facile pulizia;
- Non favoriscono la formazione di batteri, previa un’accurata pulizia ordinaria;
- Resistenza a carichi elevati;
- Resistenza all’usura e urti;
- Resistenza al transito di automezzi-carrabile (il materiale deve essere posato correttamente su fondali idonei alla destinazione d’uso).
Quando si parla di pavimentazione destinata ad ambienti per la produzione e trasformazione degli alimenti in realtà si fa riferimento a un “sistema pavimento”, all’interno del quale tutti gli elementi che compongono il sistema collaborano tra loro per soddisfare 4 requisiti fondamentali:
- SICUREZZA DEI LAVORATORI
- IGIENE per la SICUREZZA DEGLI ALIMENTI
- PENDENZE
- RESISTENZA AI CARICHI
Sicurezza dei lavoratori: i requisiti delle pavimentazioni secondo normativa e i diversi livelli di scivolosità
Secondo quanto previsto dal D.lgs. 81/08 - Testo Unico della “Sicurezza negli ambienti e luoghi di lavoro”, in merito alle pavimentazioni l’allegato IV paragrafo 1.3 specifica ai punti:
1.3.1.4. avere le superfici dei pavimenti, delle pareti, dei soffitti tali da poter essere pulite e deterse per ottenere condizioni adeguate di igiene.
1.3.2. I pavimenti dei locali devono essere fissi, stabili ed antisdrucciolevoli nonché esenti da protuberanze, cavità o piani inclinati pericolosi.
1.3.3. Nelle parti dei locali dove abitualmente si versano sul pavimento sostanze putrescibili o liquidi, il pavimento deve avere superficie unita ed impermeabile e pendenza sufficiente per avviare rapidamente i liquidi verso i punti di raccolta e scarico.
1.3.4. Quando il pavimento dei posti di lavoro e di quelli di passaggio si mantiene bagnato, esso deve essere munito in permanenza di palchetti o di graticolato, se i lavoratori non sono forniti di idonee calzature impermeabili.
Il livello di scivolosità di un pavimento è un requisito fondamentale per garantire la sicurezza della deambulazione. Come previsto dal D.lgs. 81/08, i pavimenti devono essere antisdrucciolevoli.
Il D.M. 236/89 (art.8 § 8.2.2.) prevede di misurare la scivolosità della pavimentazione in condizioni di utilizzo secondo il metodo inglese B.C.R.A. La pavimentazione è considerata antisdrucciolevole se realizzata con materiali il cui coefficiente di attrito dinamico µ > 0,40 (per elemento scivolante cuoio su pavimentazione asciutta; per elemento scivolante in gomma dura standard su pavimentazione bagnata).
Molto utilizzato, anche se non costituisce norma cogente in Italia, è il metodo di misurazione della scivolosità della pavimentazione secondo la norma tedesca DIN EN 16165 (Annex A e B).
A seconda del livello di scivolosità, che può essere legato all’uso di particolari sostanze in determinati ambienti di lavoro, o alla presenza di acqua, per la normativa tedesca è obbligatorio utilizzare un materiale a pavimento in grado di creare un notevole attrito tra le due superfici a contatto per limitare il rischio di scivolamento sulla pavimentazione. Maggiore è il gruppo di scivolosità, maggiore è la resistenza allo scivolamento.
La DIN EN 16165 Annex B stabilisce il livello di scivolosità delle superfici calpestabili per ambienti ove si cammina con piedi calzati (R9-R13) mentre la DIN EN 16165 Annex A stabilisce il livello di scivolosità delle superfici calpestabili per ambienti ove si cammina con piedi nudi (A,B,C).
Negli ambienti di lavoro destinati alla trasformazione e lavorazione degli alimenti solitamente si utilizzano pavimentazioni ceramiche con gruppo di scivolosità 9 ≤ R ≤ 12 a seconda degli ambienti e delle zone operative.
Elenco degli ambienti e delle zone operative con superfici sdrucciolevoli secondo la normativa DIN EN 16165 Annex B

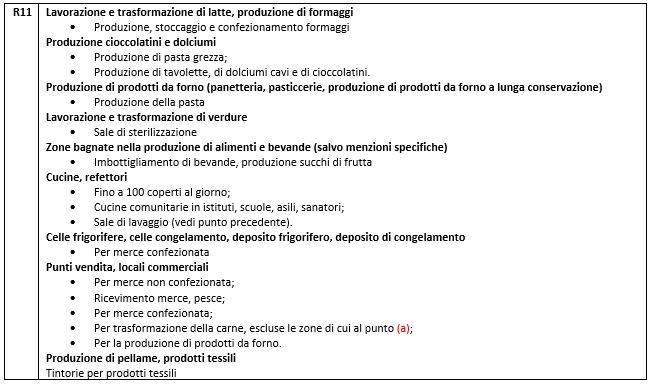
Grès porcellanato Tecnico R11 – photo courtesy Cipa Gres

Grès porcellanato tecnico R12 - photo courtesy Cipa Gres
Sicurezza degli alimenti: cosa prevede la normativa HACCP riguardo le pavimentazioni
Il sistema HACCP (acronimo dall’inglese Hazard Analysis and Critical Control Points) è un sistema di controllo preventivo degli alimenti volto a garantire elevati standard di sicurezza dal punto di vista igienico sanitario dei luoghi in cui avviene la produzione e trasformazione degli alimenti. I principi dell'HACCP possono essere applicati a tutti i settori che sono coinvolti nei processi di produzione, lavorazione e distribuzione di alimenti e bevande partendo dal settore agricolo fino ad arrivare a quello della ristorazione collettiva e della vendita al dettaglio.
Ogni azienda ha caratteristiche strutturali e produttive differenti, pertanto la documentazione HACCP non è standardizzata ma viene redatta su misura per ogni realtà, in linea quindi con la tipologia di attività svolta.
La normativa cogente sull'igiene dei prodotti alimentari è il Reg. (CE) 852/2004. Secondo quanto previsto dal documento, che conferma al suo interno il sistema HACCP come metodologia di autocontrollo, il produttore di alimenti deve prevenire ogni possibile contaminazione dei prodotti utilizzando attrezzature e pavimentazioni idonee.
Il Reg. (CE) 852/2004, Allegato II – Capitolo II “Requisiti specifici applicabili ai locali all'interno dei quali i prodotti alimentari vengono preparati, lavorati o trasformati (esclusi i locali adibiti a mensa e quelli specificati nel capitolo III)” specifica che:
1. I locali dove gli alimenti sono preparati, lavorati o trasformati (esclusi i locali adibiti a mensa e quelli specificati nel capitolo III, ma compresi i locali a bordo dei mezzi di trasporto) devono essere progettati e disposti in modo da consentire una corretta prassi igienica impedendo anche la contaminazione tra e durante le operazioni. In particolare:
a) i pavimenti devono essere mantenuti in buone condizioni, essere facili da pulire e, se necessario, da disinfettare; ciò richiede l'impiego di materiale resistente, non assorbente, lavabile e non tossico, a meno che gli operatori alimentari non dimostrino all'autorità competente che altri tipi di materiali possono essere impiegati appropriatamente. Ove opportuno, la superficie dei pavimenti deve assicurare un sufficiente drenaggio;
[…]
In linea generale, le pavimentazioni sono strutture edilizie con alto potenziale di contaminazione e devono pertanto essere realizzate con materiali omogenei, non fessurabili, facilmente lavabili e disinfettabili. Devono essere progettate per prevenire qualsiasi possibile ristagno di acqua, e se le attività prevedono un rilevante utilizzo di acqua, devono essere realizzate pendenze che convogliano i fluidi verso appositi chiusini di drenaggio. Inoltre, le giunzioni tra pavimento e pareti dovrebbero essere quanto più possibile stondate (a guscia) per facilitare la pulizia; qualsiasi cavità nei pavimenti deve essere riempita e sistemata con materiale durevole nel tempo; è necessario assicurarsi che i chiusini a pavimento siano sifonati e protetti da griglie per evitare cattivi odori e costituire punto di ingresso agli infestanti.
Un altro aspetto fondamentale da considerare nella piastrellatura sono i materiali utilizzati per le fugature. L’evoluzione tecnica degli ultimi 10 anni ha permesso di realizzare fughe completamente inassorbenti e resistenti agli acidi e alle basi, siano essi composti da resine epossidiche o in metacrilato ecc.
Il grès porcellanato è un componente del “sistema pavimento” che grazie alla sua completa greificazione (ottenuta dopo la cottura ad oltre 1.200°) determina un prodotto finito composto da una massa unica omogenea inassorbente e quindi facilmente sanificabile.
Manutenzione delle pavimentazioni in grès nel settore alimentare
Nessun pavimento è autopulente e indistruttibile! Per garantire l’igiene, la sicurezza ed essere in buono stato, i pavimenti necessitano di una corretta manutenzione.
È buona pratica eseguire la sanificazione quotidiana delle superfici e dei canali di drenaggio, effettuare un controllo dello stato di mantenimento del pavimento ed eventualmente intervenire tempestivamente in caso di usura o danneggiamento. In questo modo il pavimento avrà certamente una durata superiore alle aspettative.
Indicazioni circa la pulizia ordinaria delle superfici in grès porcellanato
Gli interventi di pulizia ordinaria delle superfici hanno lo scopo di rimuovere lo sporco, cancellare i segni e ripristinare l’aspetto originale. Le piastrelle in grès porcellanato smaltato non necessitano di trattamenti di protezione e una corretta e sistematica pulizia è sufficiente a mantenere inalterata la superficie.
Manutenzione ordinaria delle superfici - photo courtesy Cipa Gres
Un’accurata pulizia deve essere fatta con un normale lavaggio con acqua calda, straccio / spugna morbida ed eventualmente con l’utilizzo di detergenti neutri. Per locali con grandi superfici possono essere utilizzate macchine industriali lavasciuga con completamento manuale dove necessario.
Raccomandazioni:
- Evitare di strofinare le superfici con strumenti abrasivi, come pagliette in metallo o spazzole dure, che potrebbero lasciare graffi e segni indelebili;
- Rimuovere eventuali residui grassi o oleosi con detergenti contenenti solventi organici o con detergenti alcalini (pH>9) e fare seguire un accurato risciacquo;
- Evitare l’utilizzo di saponi in quanto tendono a lasciare uno strato viscido, in particolare se utilizzati in abbinamento ad acque dure;
- Non utilizzare prodotti contenenti cere o brillantanti;
- Evitare l’uso di detergenti abrasivi su superfici lucide e/o levigate; possono essere utilizzati su materiali matt., previa verifica su una piccola porzione piastrellata.
In generale l’uso di qualunque detergente non neutro deve essere preliminarmente testato su una piastrella non posata o su una porzione nascosta della pavimentazione.
Pendenze nelle pavimentazioni: il drenaggio è un requisito fondamentale per evitare ristagni d’acqua
Come già anticipato nel paragrafo precedente, una pavimentazione industriale per uso alimentare dovrà scaricare in maniera agevole tutti i liquidi residui di lavorazioni o liquidi di lavaggio verso chiusini di drenaggio a pavimento.
L’esperienza maturata in tanti anni di attività delle più importanti aziende del settore di progettazione e posa delle pavimentazioni industriali con finitura gres porcellanato tecnico indica come pendenza minima il valore del 1% da realizzarsi in zone bagnate della lavorazione.
Resistenza al carico di compressione del grès porcellanato tecnico
Il grès porcellanato tecnico impiegato nella realizzazione di un pavimento destinato all’industria alimentare deve avere un’elevata resistenza meccanica a compressione tale da resistere ai mezzi di movimentazione, come ad esempio i carraelli elevatori .
Nella progettazione di una qualsiasi pavimentazione è fondamentale che il prodotto utilizzato sia in grado di resistere a sollecitazioni, sia statiche che dinamiche che possono raggiungere entità molto elevate. Lo spessore della piastrella svolge un ruolo fondamentale per la resistenza a tali sollecitazioni.
Il carico di rottura è un parametro che serve per valutare la capacità della mattonella di sopportare carichi statici e dinamici quando è posta in esercizio. La norma considera la piastrella come una trave, posta su due rulli distanti tra loro, mentre al centro viene applicata una forza tramite un terzo rullo. Il carico di rottura è il peso che viene sopportato prima della rottura a flessione della mattonella.
Istruzioni per la progettazione, installazione e manutenzione secondo norma UNI 11493-1
La norma UNI 11493-1 definisce la qualità e le prestazioni di una piastrellatura ceramica, fornisce regole ed istruzioni da osservare nella scelta dei materiali, nella progettazione, nell’installazione nell’impiego e manutenzione, e specifica soluzioni conformi tipiche, tali da assicurare il raggiungimento ed il mantenimento nel tempo dei livelli richiesti di qualità e prestazioni. La UNI 11493-1 si applica alle piastrellature ceramiche a pavimento e a parete, interne ed esterne, installate principalmente con adesivi, ma anche con malta cementizia o altri sistemi.
Come procedere nella posa in opera della pistrellatura ceramica
Prima di iniziare le operazioni di posa di una qualsiasi superficie si raccomanda di accertarsi che la partita di materiale sia adeguata e sufficiente per quantità, tono e calibro, a quella necessaria. Si dovranno poi seguire tutte le norme e le precauzioni che sono alla base di una corretta esecuzione del lavoro (preparazione del sottofondo, composizione della malta o dei collanti, rispetto dei tempi di essicazione, posizionamento dei giunti di dilatazione, battitura, ect.).
Posa piastrellatura con adesivi
La posa deve essere effettuata da personale qualificato con l’ausilio di attrezzi adeguati. La superficie su cui si effettua la posa (massetto) deve essere perfettamente piana. La tolleranza massima imposta dalla norma +/- 3mm per un dislivello determinato sotto un regolo di 2m. La superficie su cui si effettua la posa deve essere ben stagionata, priva di polvere e di fessurazioni visibili.
Durante l’operazione di posa è vivamente consigliato l’utilizzo di un’adeguata illuminazione.
La scelta dell’adesivo è condizionata dalla tipologia delle piastrelle (gruppo di appartenenza e formato), dal tipo di superficie da rivestire e dalla sua destinazione d’uso.
È opportuno verificare la posa del materiale prima che il collante sia secco, per facilitare eventuali correzioni.
Posa piastrellatura con malta fresca
La posa a malta cementizia fresca o “strato spesso” è sconsigliata per formati aventi lato > 30 cm e con supporti non assorbenti.
Realizzazione dei giunti di dilatazione o fughe nelle pavimentazioni ceramiche
I giunti di dilatazione sono elementi molto importanti per il mantenimento di una buona superficie piastrellata e si consiglia di avvalersi della collaborazione e/o consulenza di un posatore professionista che realizzerà i giunti rispettando una campitura secondo la conformazione dell’area da piastrellare e in linea di massima creando quadrati con lati simili con misura di circa 5x5m lineari.
Per la fuga/giunto tra piastrella e piastrella si considera posa a “giunto minimo” quella con fuga a 2 mm.
I giunti devono essere posizionati:
- Su raccordi strutturali (giunti strutturali);
- tra suolo e parete (giunti perimetrali);
- tra una piastrella e l’altra (giunti di posa o fuga);
- tra piastrelle ed altri materiali (es. accostamento ceramica/linoleum/legno).
Stuccatura superficie posata
Prima di realizzare le fughe è consigliabile attendere fino a completa asciugatura del collante e assicurarsi che i giunti di posa siano vuoti e liberi da ogni traccia di collante e/o polveri. Stuccare piccole superfici per volta (4-5 mq), per la stuccatura con prodotti epossidici non stuccare oltre 2 mq per volta e procedere immediatamente alla pulizia.
Eliminare l’eccesso di fugante dalla superficie con movimenti diagonali quando il prodotto è ancora umido e togliere tutti i residui, in particolar modo per le superfici da esterno.
Pulire accuratamente con una spugna bagnata in acqua limpida e pulita e ripassare con straccio umido su tutta la superficie fughe comprese. Per fughe in netto contrasto cromatico con le piastrelle posate è consigliabile testare il fugante su un’area circoscritta e nascosta.
Per gli stucchi epossidici si raccomanda la pulizia con spugna e abbondante acqua. La velocità di reazione e indurimento di questi prodotti rende impossibile la rimozione dei residui successivamente all’indurimento. Il giorno dopo la stuccatura effettuare una pulizia completa con detergente alcalino.
Si consiglia di consultare i produttori di materiale fugante per verificare la scelta corretta della fuga rispetto al tipo di piastrella.
Pulizia e manutenzione post posa
Un cantiere si può considerare completamente finito quando è sgombro da qualunque utensile/materiale derivante dalle lavorazioni. Per ridurre i rischi di danneggiamento della superficie piastrellata, è necessario proteggerla ed evitare il più possibile la presenza di materiali abrasivi (polveri o residui da lavorazioni successive).
Il lavaggio dopo la posa è un una fase di fondamentale importanza per tutti gli interventi successivi e per una corretta manutenzione. Un accurato lavaggio iniziale permette ai pavimenti di restare belli e protetti a lungo e si esegue normalmente una sola volta prima dell’utilizzo del pavimento.
Si raccomanda di effettuare la pulizia iniziale dopo 4-5 giorni e non più tardi di 10, dalla posa e stuccatura della superficie. La superficie fugata e pulita può presentare un film di residui cementizi che non sono asportabili con sola acqua per cui si rende necessario l’utilizzo di un prodotto a base acida, opportunamente diluito (diluizione da 1:10 a 1:4 in acqua fredda), in base a quanto dichiarato dal produttore. Per gli stucchi epossidici i produttori forniscono appositi detergenti.
La prima operazione da eseguire è quella di bagnare la superficie piastrellata ed in particolare le fughe (di norma non resistenti agli acidi). Spargere la soluzione acida preparata e lasciare agire per un breve tempo (2 min.).
Non lasciare asciugare il prodotto applicato. Procedere alla rimozione della soluzione aiutandosi con una macchina mono spazzola (disco non abrasivo), aspira liquidi, altri mezzi e/o manualmente e alla fine risciacquare abbondantemente.
È importante sottolineare che la pulizia eseguita con macchine (particolarmente consigliata per prodotti strutturati e per grandi superfici), va sempre completata manualmente nei punti difficilmente raggiungibili, soprattutto negli angoli, lungo le pareti dei locali e in ogni zona in cui la mono spazzola non può operare.
È sempre consigliabile testare la resistenza del prodotto agli acidi su un pezzo non posato o su una piccola porzione nascosta della superficie piastrellata; in particolare per prodotti lappati o levigati.
L’uso di prodotti di pulizia contenenti acido fluoridrico (HF) e suoi derivati sono da evitare.
Consigli di posa a seconda della tipologia dei formati
Per i formati rettangolari, oltre alla posa ortogonale, si consiglia la posa a correre, regolare o irregolare, con una differenza tra pezzo e pezzo di max 1/3 per formati: 10x20 - 12.5x25 - 15x30 - 30x60.
Esistono anche formati esagonali in grès porcellanato tecnico antiacido la cui particolare forma permette ai mezzi di movimentazione di non incontrare mai le fughe garantendo di fatto una maggior resistenza alla pavimentazione.
Grès porcellanato tecnico - photo courtesy Cipa Gres
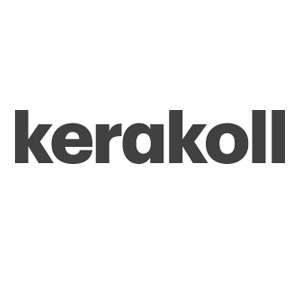
Ceramica
Ceramica: tutto su pavimenti e rivestimenti, adesivi, posa, patologie, manutenzione e design. Articoli tecnici e di tendenza per progettisti, imprese, applicatori e professionisti delle finiture.
Normativa Tecnica
Con questo TOPIC raccogliamo le news e gli approfondimenti che riguardano il tema della normativa tecnica: le nuove disposizioni, le sentenze, i pareri e commenti, l’analisi di casi concreti, il commento degli esperti.
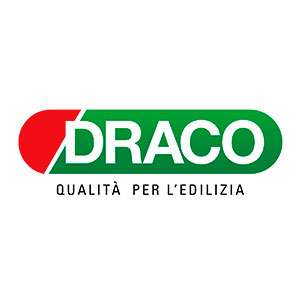
Pavimenti Industriali
Con il topic "pavimento industriale" vengono raccolti tutti gli articoli pubblicati sul Ingenio su queste tipologie di pavimentazioni in calcestruzzo e riguardanti la normativa, la progettazione, l'applicazione, l'innovazione tecnica, i casi studio, i controlli e i pareri degli esperti.

Pavimenti per Interni
Tutto quello che devi sapere sulle pavimentazioni per interni: le tipologie di rivestimento più comuni, le soluzioni tecniche più innovative, gli...

Progettazione
La progettazione costituisce un passaggio fondamentale nell’intero processo edilizio, poiché determina in maniera significativa la qualità, la...
Condividi su: Facebook LinkedIn Twitter WhatsApp